Biodegradable coolants have emerged as a sustainable alternative to conventional automotive coolants, offering superior cooling performance while minimizing environmental impact and toxicity risks. This comprehensive article explores the composition, biodegradability, cooling capabilities, service life, corrosion protection, environmental impact, unique characteristics, formulation specifics, top brands, and purchasing considerations of these eco-friendly coolants.
Blown Brake Line Brake Symptoms: Signs of a Leaking Brake Line & What to Do
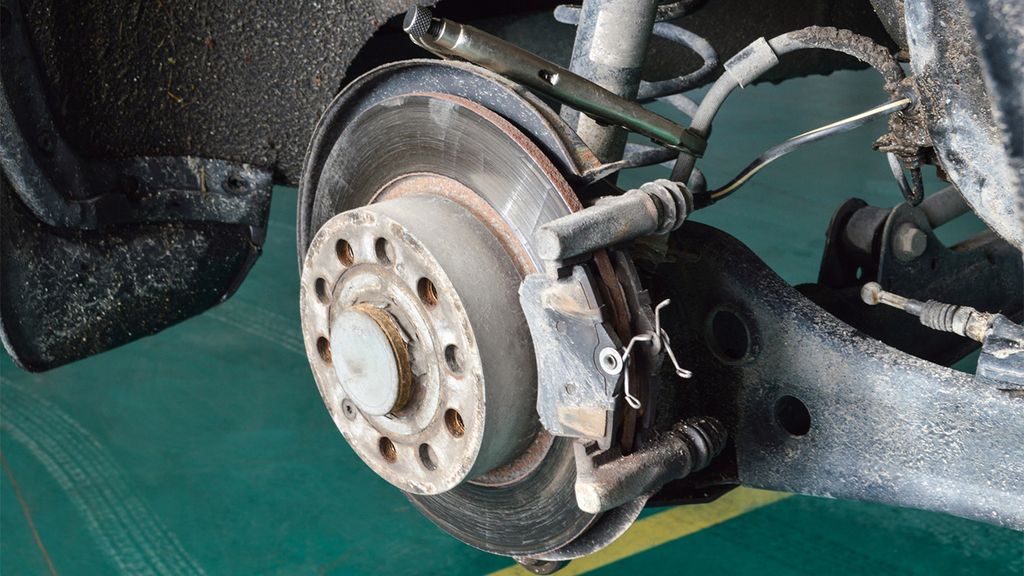
Blown Brake Line Brake Symptoms: Signs of a Leaking Brake Line & What to Do
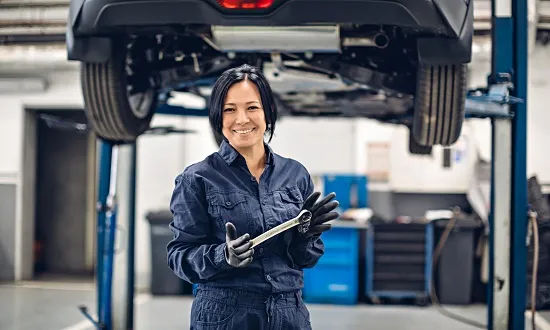
Introduction
The braking system is one of the most critical safety components in a vehicle. Its primary function is to slow down or stop the vehicle in a controlled and efficient manner, ensuring the safety of the driver, passengers, and other road users. A properly functioning brake system is essential for maintaining control and stability, especially in emergency situations or when navigating through challenging road conditions.
Understanding the Causes
Brake lines are subjected to various environmental and operational stresses, which can lead to their failure over time. Here are the main causes of a blown or leaking brake line:
Cause | Description |
---|---|
Corrosion and Rust | The steel brake lines are constantly exposed to moisture, road salt, and other corrosive elements, weakening the metal and eventually causing cracks, holes, or complete failure. |
Physical Damage | Road debris, rocks, or rubbing against other components can cause abrasions, dents, or punctures in the line, resulting in fluid leaks. |
Age and Wear | The rubber hoses can become brittle and crack, while the steel lines can weaken and fail after many years of use and exposure to high brake fluid pressure. |
Improper Installation | If brake lines are not installed correctly or are bent too sharply, it can cause strain and eventual failure of the line. |
Contaminated Brake Fluid | Using the wrong type of brake fluid or contaminated fluid can cause the brake lines and hoses to swell, degrade, or become damaged from the inside. |
Corrosion and rust are among the most common culprits, as the steel brake lines are constantly exposed to moisture, road salt, and other corrosive elements. This weakens the metal over time, eventually causing cracks, holes, or complete failure of the brake line.
Physical damage is another frequent cause of blown brake lines. Road debris, rocks, or even rubbing against other components can cause abrasions, dents, or punctures in the line, resulting in fluid leaks. Age and wear also play a significant role, as the rubber hoses can become brittle and crack, while the steel lines can weaken and fail after many years of use and exposure to high brake fluid pressure.
Improper installation or maintenance can also contribute to brake line issues. If the lines are not installed correctly or are bent too sharply, it can cause strain and eventual failure. Additionally, using the wrong type of brake fluid or contaminated fluid can cause the brake lines and hoses to swell, degrade, or become damaged from the inside.
Inspecting and Identifying Brake Line Issues
As a mechanic, I always emphasize the importance of regular brake system inspections. During these inspections, I follow a thorough process to identify any potential brake line issues:
Visually inspect all brake lines and hoses for any signs of cracks, bulges, leaks, or physical damage.
Check for rust, corrosion, or moisture around the brake lines, especially near connections and bends.
Gently squeeze the rubber brake hoses to check for firmness. Soft or spongy hoses may indicate internal damage or collapse.
Check the brake fluid level and condition in the master cylinder reservoir. Low fluid levels or contaminated fluid can indicate a leak.
During a test drive, pay attention to any signs of reduced braking performance, pulling to one side, or a spongy brake pedal feel.
Specific signs of damage that I look for include:
Sign | Description |
---|---|
Leaks | Brake fluid dripping or puddles under the vehicle near a wheel are a clear sign of a brake line leak. |
Corrosion/Rust | Flaking, pitting, or excessive rust on the brake lines indicates advanced corrosion and potential failure. |
Bulges/Cracks | Bulges or cracks in the rubber brake hoses are signs of internal damage or imminent failure. |
Physical Damage | Dents, punctures, or abrasions on the brake lines can lead to leaks or complete failure. |
During the inspection process, I carefully examine each component of the brake system, looking for any signs of wear, damage, or potential failure. This thorough inspection is crucial for identifying and addressing any issues before they become a safety hazard.
Repairing Brake Line Issues
When it comes to repairing brake line issues, the approach varies depending on the extent and location of the damage. Here are some common repair procedures I follow:
Replacing a Section of Brake Line
Safely raise and support the vehicle to access the damaged section of the brake line.
Use a brake line cutter or tubing cutter to remove the damaged section.
Measure and cut a new section of brake line, leaving enough length for flaring.
Use a brake line flaring tool to create a double flare on each end of the new line.
Install the new brake line section, using new crush washers and fittings as needed.
Bleed the brake system to remove any air, ensuring proper operation.
Replacing a Rubber Brake Hose
Raise and support the vehicle to access the damaged brake hose.
Use a line wrench to loosen the fittings at each end of the hose.
Install the new brake hose, using new crush washers if needed.
Tighten the fittings securely, but avoid over-tightening, which can damage the hose.
Bleed the brake system thoroughly to remove any air.
Throughout these repair procedures, I follow a few essential tips and cautions:
Use only DOT-approved brake lines and hoses designed specifically for the vehicle.
Double flare both ends of new brake lines for a secure, leak-free connection.
Replace crush washers whenever disconnecting brake line fittings.
Avoid kinking or bending brake lines too sharply during installation, as this can cause future issues.
Bleed the brake system thoroughly after any brake line repair to ensure proper operation.
Preventing Future Brake Line Issues
While repairs are sometimes necessary, prevention is always the best approach. As a mechanic, I recommend regular maintenance and proper usage to help prevent brake line issues:
Regular Maintenance
Inspect brake lines and hoses during routine maintenance intervals or annually.
Replace brake fluid as recommended by the manufacturer to prevent contamination.
Keep the undercarriage clean and free of debris that could damage brake lines.
Proper Usage and Operation
Avoid aggressive braking or riding the brakes, which can cause excessive heat and wear.
Be cautious when driving over rough terrain or obstacles that could damage brake lines.
Address any signs of brake issues promptly to prevent further damage.
By following these preventive measures, you can help extend the life of your brake lines and avoid costly repairs or potential safety hazards.
Cost Considerations
The cost of repairing or replacing brake lines can vary depending on the extent of the damage and the specific vehicle. Here are some general cost estimates:
Repair | Cost Range |
---|---|
Replacing a single brake line section | $100 - $300 (including parts and labor) |
Replacing a rubber brake hose | $50 - $150 (including parts and labor) |
Complete brake line replacement (all four lines) | $500 - $1,000 (including parts and labor) |
While these costs may seem significant, it's important to address brake line issues promptly. The cost of repairs can escalate if left unattended, and faulty brakes can compromise your safety on the road. As a mechanic, I always recommend prioritizing brake system repairs to ensure your vehicle's safe operation.
Conclusion
Dealing with blown brake lines is a common challenge in the automotive world, but with the right knowledge and expertise, it's a problem that can be effectively addressed. As a mechanic, I've seen firsthand the importance of regular inspections, proper repair procedures, and preventive maintenance in keeping your brake system in top condition.
Remember, your safety on the road is paramount, and a well-maintained brake system is crucial. If you ever suspect a brake line issue, don't hesitate to have it inspected and repaired by a qualified mechanic. By following the best practices outlined in this article, you can help prevent blown brake lines and ensure a safe and reliable driving experience.
FAQs
What causes brake lines to fail?
The most common causes of brake line failure are corrosion/rust, physical damage, age and wear, improper installation, and contaminated brake fluid.
How can I inspect brake lines for issues?
Visually inspect all brake lines and hoses for cracks, bulges, leaks, rust, corrosion, moisture, and physical damage. Also check brake fluid level and condition.
What are the signs of brake line damage?
Common signs include brake fluid leaks/puddles, excessive rust/corrosion on lines, bulges/cracks in hoses, and physical damage like dents or punctures.
How do you repair a damaged brake line section?
Cut out the damaged section, measure and install a new flared section using a brake line flaring tool, and bleed the system.
How do you replace a rubber brake hose?
Loosen the fittings, install the new hose using new crush washers if needed, tighten fittings securely, and bleed the system.
What tips should I follow when repairing brake lines?
Use DOT-approved lines/hoses, replace crush washers, avoid kinks/sharp bends, and thoroughly bleed the system after repairs.
How can I prevent future brake line issues?
Regularly inspect lines/hoses, replace brake fluid as recommended, keep the undercarriage clean, and avoid aggressive braking.
What tools are needed for brake line repairs?
Line wrenches, flaring kit, replacement lines, fittings, line cutter, bender, files, brake fluid, and jack are typically required.
Where should I disconnect brake lines first?
It's recommended to disconnect brake lines at the wheel end first before the ABS pump/master cylinder end.
Do I need to plug ABS ports when lines are disconnected?
Yes, using special plugs or caps on the ABS ports can prevent brake fluid leaks and contamination when lines are removed.
Bình luận (0)
Bài viết đề xuất
As an automotive mechanic with years of experience, I’ve encountered a wide range of engine issues, but one that often puzzles many is the P0362 code. This code indicates a problem with the Ignition Coil 'L' Primary Control Circuit/Open, specifically for cylinder #12 in a V12 engine configuration. Let’s dive into the details of what this code means, its common causes, how to diagnose it, and the steps to fix it.
Maintaining a vehicle's braking system is crucial for ensuring safety on the road. One of the critical components that require regular inspection and timely replacement is the brake lines
Greetings, fellow automotive enthusiasts! As an experienced mechanic, I've encountered numerous diagnostic trouble codes (DTCs) throughout my career, but one that always piques my interest is the P0378. This code indicates an issue with the high-resolution timing reference signal B, which plays a crucial role in ensuring your engine's precise timing. In this comprehensive article, I'll delve into the intricacies of this code, its causes, diagnosis, and repair procedures, sharing insights from my hands-on experience in the automotive repair world.