Automotive exhaust systems play a crucial role in managing emissions and ensuring optimal vehicle performance. Among the various materials used in their construction, aluminized steel has emerged as a popular choice, offering a compelling balance of corrosion resistance, durability, and cost-effectiveness
Friction Reduction Additives: Unlocking Efficiency and Longevity for Automotive Applications
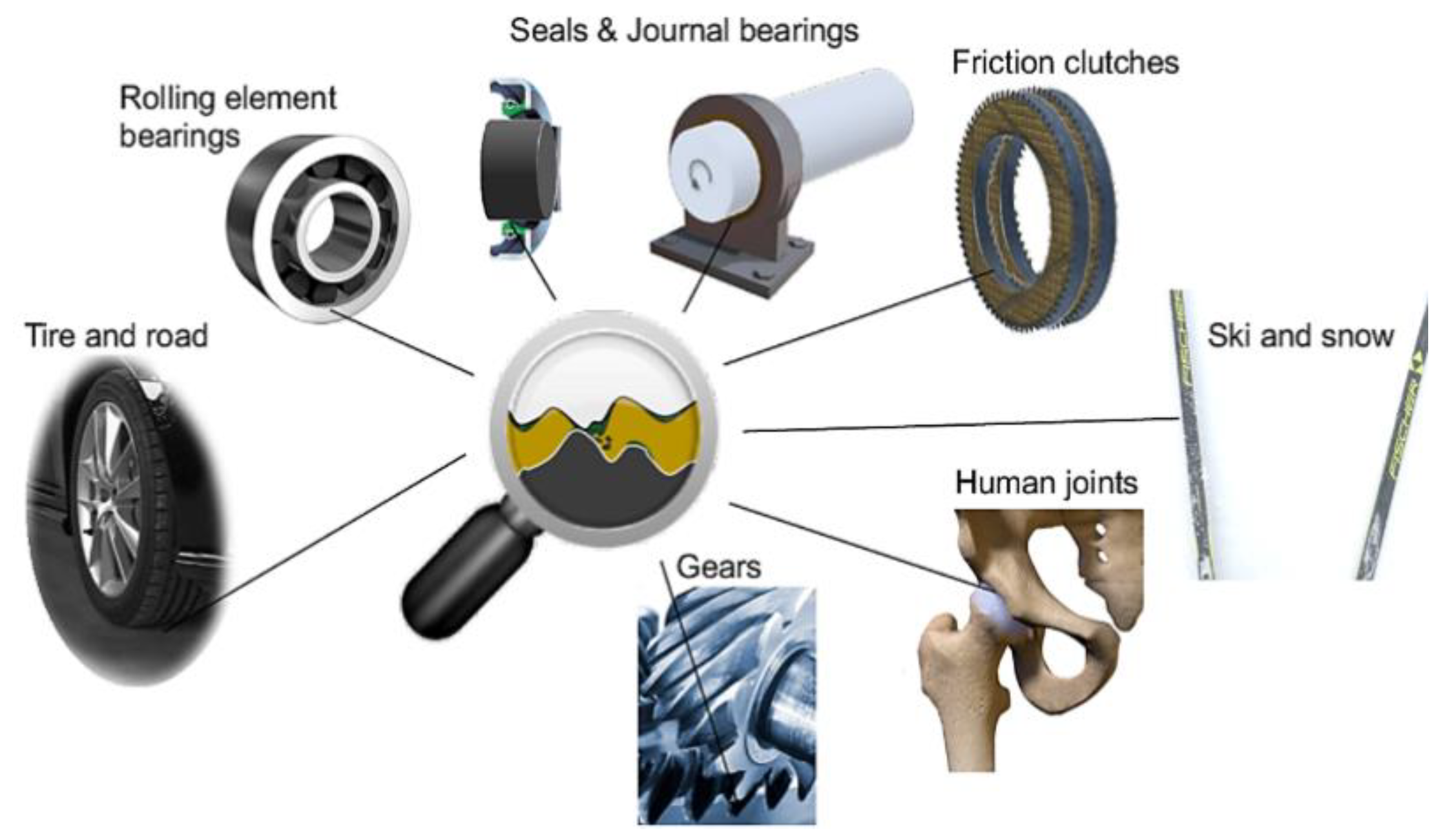
Friction Reduction Additives: Unlocking Efficiency and Longevity for Automotive Applications
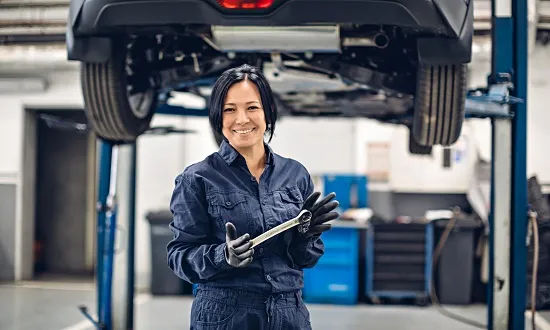
Friction is an inherent force that opposes the relative motion between surfaces in contact, leading to energy losses and accelerated wear. In the automotive industry, minimizing friction is crucial for improving fuel efficiency, extending component life, and reducing maintenance costs. This is where friction reduction additives come into play, offering innovative solutions to enhance the performance and durability of automotive systems.
This comprehensive article delves into the world of friction reduction additives, exploring their types, working mechanisms, applications, and the latest advancements in this field. We will uncover the science behind these specialized compounds and their role in optimizing automotive lubrication, ultimately contributing to a more sustainable and efficient driving experience.
Types of Friction Reduction Additives
Friction reduction additives encompass a diverse range of chemical compounds, each with unique properties and mechanisms of action. Understanding their characteristics is essential for selecting the appropriate additive for specific automotive applications.
Here are the main types of friction reduction additives:
Additive Type | Description |
---|---|
Organic Friction Modifiers (OFMs) | Amphiphilic molecules that form protective films on metal surfaces, with a polar head group adsorbing onto the metal and a lipophilic hydrocarbon tail aligning outward into the lubricating oil, creating a low-friction surface. Examples include glycerol monooleate and fatty acid esters. |
Organomolybdenum Friction Modifiers (MFMs) | Additives that form nano-sized sheets dispersed in a carbon or pyrite matrix, which orient themselves in layers and slide against each other, reducing friction. Molybdenum dithiocarbamate (MoDTC) is a prominent example. |
Polymer-based Friction Modifiers | Functionalised polymers, such as polyalkylene glycols (PAGs), that exhibit a strong affinity for metal surfaces due to their polarity, forming durable, low-friction lubricating films. |
Hybrid Friction Modifiers | Developed by CIDETEC, these additives combine lamellar chalcogenide nanoparticles (e.g., MoS2, WS2) with organic moieties, resulting in a unique combination that significantly improves tribological performance. |
Organic Friction Modifiers (OFMs)
Organic friction modifiers (OFMs) are amphiphilic molecules that form protective films on metal surfaces. These additives possess a polar head group that adsorbs onto the metal surface and a lipophilic hydrocarbon tail that aligns outward into the lubricating oil. This unique molecular structure creates a low-friction surface, reducing the direct metal-to-metal contact and minimizing wear.
Examples of OFMs include glycerol monooleate and fatty acid esters. These compounds are widely used in engine oils, transmission fluids, and other automotive lubricants due to their ability to improve fuel economy and extend component life.
Organomolybdenum Friction Modifiers (MFMs)
Organomolybdenum friction modifiers (MFMs) are a class of additives that form nano-sized sheets dispersed in a carbon or pyrite matrix. These sheets orient themselves in layers, allowing them to slide against each other and effectively reduce friction. Molybdenum dithiocarbamate (MoDTC) is a prominent example of an MFM, commonly used in automotive lubricants.
MFMs are particularly effective in boundary lubrication conditions, where the lubricant film is thin or non-existent, making them valuable for applications such as engine components and transmission gears.
Polymer-based Friction Modifiers
Polymer-based friction modifiers are functionalised polymers that exhibit a strong affinity for metal surfaces due to their polarity. These additives form durable, low-friction lubricating films on metal surfaces, providing excellent wear protection and friction reduction.
Polyalkylene glycols (PAGs) are a widely used class of polymer-based friction modifiers in automotive lubricants. Their ability to form stable films and their compatibility with various lubricant formulations make them versatile additives for a range of automotive applications.
Hybrid Friction Modifiers
Hybrid friction modifiers represent a cutting-edge development in the field of friction reduction additives. Developed by CIDETEC, these additives combine lamellar chalcogenide nanoparticles, such as molybdenum disulfide (MoS2) or tungsten disulfide (WS2), with organic moieties.
This unique combination results in a synergistic effect, significantly improving the tribological performance of lubricants and composite materials. Hybrid friction modifiers offer superior friction reduction capabilities and enhanced wear protection, making them ideal for high-performance automotive applications.
Working Mechanisms of Friction Reduction Additives
The effectiveness of friction reduction additives lies in their ability to form protective films or layers on metal surfaces, reducing direct metal-to-metal contact and providing a low-shear interface. However, the specific mechanisms vary depending on the additive type.
Film Formation and Adsorption
Organic friction modifiers (OFMs) and polymer-based friction modifiers work by forming dense monolayers or thick, reacted viscous layers on metal surfaces. In the case of OFMs, the hydrocarbon tails align vertically, creating a low-friction surface. Polymer-based additives, on the other hand, form durable, low-friction lubricating films due to their polarity and affinity for metal surfaces.
Layered Nanostructures
Organomolybdenum friction modifiers (MFMs) and hybrid friction modifiers rely on the formation of layered nanostructures. MFMs form nano-sized sheets that orient themselves in layers, allowing them to slide against each other and reduce friction. Hybrid friction modifiers combine lamellar chalcogenide nanoparticles with organic moieties, resulting in a unique combination that enhances their tribological performance.
Tribochemical Reactions
In addition to physical mechanisms, some friction reduction additives undergo tribochemical reactions on the metal surface, contributing to their effectiveness. For example, organomolybdenum compounds can undergo chemical reactions, forming molybdenum disulfide (MoS2) sheets that provide excellent lubricity and wear protection.
Applications in the Automotive Industry
Friction reduction additives find widespread applications in various automotive systems, contributing to improved fuel efficiency, reduced wear, and extended component life.
Engine Oils: Formulated with friction reduction additives to minimize friction between moving parts, such as pistons, bearings, and valvetrain components, improving fuel economy, reducing emissions, and extending engine life.
Transmission Fluids: Automatic and manual transmission fluids benefit from these additives, reducing friction between gears, clutches, and other components, improving shifting performance and extending transmission lifespan.
Gear Oils: Used in differentials, transfer cases, and other automotive gearboxes, these additives minimize gear wear, reduce power losses, and improve overall efficiency, contributing to better fuel economy and longer component life.
Greases and Chassis Lubricants: Essential for lubricating suspension components, wheel bearings, and other automotive components subjected to high loads and extreme conditions, these additives help reduce friction, minimize wear, and extend service life.
Performance and Effectiveness
The effectiveness of friction reduction additives in improving fuel economy and reducing wear has been well-documented through extensive research and testing.
Fuel Economy Improvements
Studies have shown that organic friction modifiers and organomolybdenum additives can provide fuel economy improvements ranging from a few tenths of a percent to over 1% in standardized engine tests. These improvements may seem small, but they can translate into significant savings over the lifetime of a vehicle, especially for commercial fleets and heavy-duty vehicles.
Friction Coefficient Reduction
CIDETEC's hybrid friction modifiers have demonstrated remarkable performance, achieving over 50% reduction in friction coefficient compared to commercial oils without these advanced additives. This substantial reduction in friction can lead to significant energy savings and extended component life in various automotive applications.
Additive Type | Fuel Economy Improvement | Friction Coefficient Reduction |
---|---|---|
Organic Friction Modifiers | Up to 1% | - |
Organomolybdenum Friction Modifiers | Up to 1% | - |
Hybrid Friction Modifiers | - | Over 50% |
Influencing Factors
It is important to note that the performance of friction reduction additives can be influenced by various factors, such as:
Lubricant formulation
Engine design
Operating conditions
Interactions with other additives in the lubricant package
Careful selection and compatibility testing are crucial to ensure optimal performance and avoid any adverse effects.
Environmental and Safety Considerations
While friction reduction additives offer significant benefits, it is essential to consider their potential environmental and safety implications.
Environmental Impact
Some additives, such as organomolybdenum compounds, may raise concerns regarding toxicity and environmental impact. Manufacturers and users should follow appropriate handling and disposal guidelines to mitigate any risks and ensure compliance with environmental regulations.
Safety Considerations
Certain friction reduction additives may pose health and safety risks if not handled properly. Appropriate personal protective equipment (PPE) and safe handling practices should be implemented to minimize exposure risks during manufacturing, transportation, and use.
Future Trends and Developments
The development of friction reduction additives is an active area of research, with ongoing efforts to improve their performance, reduce environmental impact, and explore new applications.
Emerging Technologies
Emerging technologies, such as CIDETEC's hybrid friction modifiers, demonstrate the potential for innovative solutions that combine the advantages of different additive types. These advanced additives offer superior tribological performance while addressing environmental concerns and meeting the demanding requirements of modern automotive systems.
Tailored Solutions
Research is underway to develop friction reduction additives specifically tailored for elastohydrodynamic lubrication conditions, which are prevalent in applications like bearings and gears. These tailored solutions could further enhance energy efficiency and component life in critical automotive systems.
Sustainable Formulations
As environmental concerns continue to gain prominence, the development of environmentally friendly and sustainable friction reduction additives is a priority. Researchers are exploring bio-based and biodegradable alternatives, as well as additives with reduced toxicity and improved eco-friendliness.
Conclusion
Friction reduction additives play a vital role in improving the performance and efficiency of automotive systems. By reducing friction between moving surfaces, these specialized compounds contribute to improved fuel economy, extended component life, and reduced energy consumption.
As the automotive industry continues to evolve, with a focus on sustainability and efficiency, the importance of friction reduction additives will only increase. Through ongoing research and development, these additives are poised to offer innovative solutions that address environmental concerns while delivering superior tribological performance across diverse automotive applications.
FAQs
What are the main types of friction reduction additives discussed?
The main types are organic friction modifiers (OFMs), organomolybdenum friction modifiers (MFMs), polymer-based friction modifiers, and hybrid friction modifiers.
How do organic friction modifiers (OFMs) work?
OFMs are amphiphilic molecules that form protective low-friction films on metal surfaces by adsorbing the polar head group onto the metal and aligning the hydrocarbon tail outwards.
What is the role of organomolybdenum friction modifiers (MFMs)?
MFMs react to form nano-sized sheets dispersed in a matrix, which orient themselves in layers and slide against each other, reducing friction.
How do polymer-based friction modifiers function?
Functionalised polymers like polyalkylene glycols exhibit strong affinity for metal surfaces due to their polarity, forming durable low-friction lubricating films.
What are hybrid friction modifiers?
Hybrid friction modifiers combine lamellar chalcogenide nanoparticles (e.g., MoS2, WS2) with organic moieties, resulting in superior tribological performance.
What are the main applications of friction reduction additives in the automotive industry?
They are used in engine oils, transmission fluids, gear oils, greases, and chassis lubricants to improve fuel efficiency, reduce wear, and extend component life.
How effective are friction reduction additives in improving fuel economy?
Studies show organic and organomolybdenum additives can provide fuel economy improvements ranging from a few tenths of a percent to over 1%.
What are the environmental and safety considerations for friction reduction additives?
Some additives may raise toxicity and environmental impact concerns, requiring proper handling and disposal. Appropriate personal protective equipment should be used.
What are some emerging trends in friction reduction additives?
Emerging trends include hybrid friction modifiers, tailored solutions for specific lubrication conditions, and the development of environmentally friendly and sustainable bio-based alternatives.
How do friction reduction additives contribute to engine durability?
By reducing friction and wear, these additives help extend the lifespan of engine components, contributing to overall engine durability and reliability.
Bình luận (0)
Bài viết đề xuất
As an automotive mechanic with years of experience, I've encountered numerous diagnostic trouble codes (DTCs). One that often puzzles many is the P0360 code, which indicates an issue with the ignition coil "J" primary control circuit. In this article, I'll walk you through the intricacies of this code, its causes, how to diagnose it, and the steps to fix it. Let's dive in!
As a driver, it's essential to pay attention to your vehicle's warning lights, especially when it comes to the brake system. If you've noticed that your brake light is staying on, even when the parking brake is released, it's crucial to investigate the cause promptly. A persistent brake light can indicate several issues, ranging from minor to severe, and it's important to address them to ensure your safety on the road.
Howdy, folks! As an automotive mechanic with years of experience under my belt, I've encountered my fair share of diagnostic trouble codes. Today, we're going to dive deep into the mysterious world of the P0384 code – "Glow Plug Control Module 1 Control Circuit High." Now, I know what you're thinking, "Glow plugs? Isn't that something from the Stone Age?" Well, let me tell you, these little guys are still kicking and playing a crucial role in modern diesel engines.
Bài viết liên quan
The world is rapidly transitioning towards sustainable practices, and the automotive industry is no exception. As environmental concerns grow, the demand for eco-friendly alternatives to traditional petroleum-based products has surged.
The automotive industry is constantly evolving, driven by the pursuit of enhanced performance, efficiency, and sustainability
Graphene, a two-dimensional carbon allotrope, has garnered significant attention due to its exceptional properties, including high electrical and thermal conductivity, mechanical strength, and large surface area. Ionic liquids (ILs), on the other hand, are molten salts composed of organic cations and inorganic or organic anions, known for their unique properties such as negligible vapor pressure, high thermal stability, and tunable physicochemical properties.
Low-friction oils have emerged as a game-changer, offering a multitude of benefits across various industries. These specialized lubricants are designed to reduce friction, minimize wear, and optimize performance, contributing to improved fuel economy, extended equipment life, and a reduced environmental footprint.