The internal combustion engine, a marvel of engineering that revolutionized transportation and industry, was not the brainchild of a single inventor. Its development was a collaborative effort spanning decades, with numerous pioneers contributing their ingenuity and innovations.
How Does a Torque Wrench Work? A Comprehensive Guide to Precise Tightening
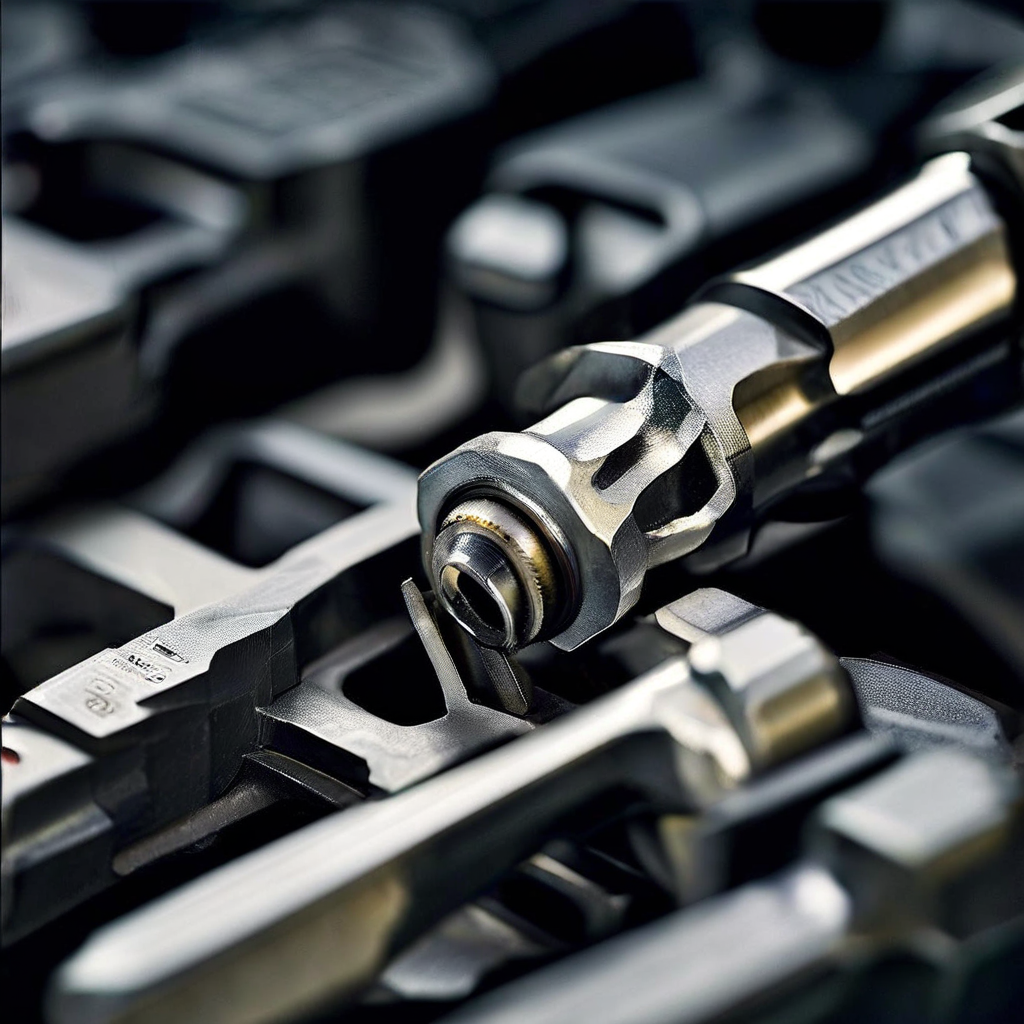
How Does a Torque Wrench Work? A Comprehensive Guide to Precise Tightening
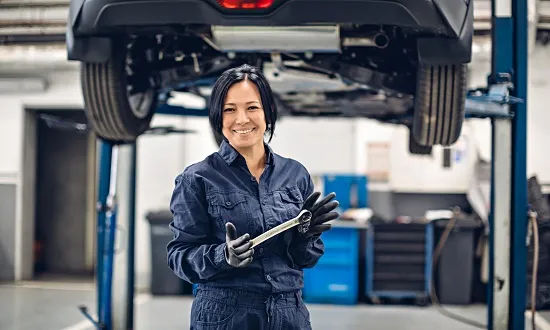
In the world of automotive repair, construction, and manufacturing, achieving precise tightening of fasteners is crucial for optimal performance and preventing potential failures. This comprehensive guide delves into the intricate workings of a torque wrench, a specialized tool designed to apply a specific rotational force to nuts, bolts, and other threaded components. By understanding the different types, working principles, calibration techniques, and proper usage methods, you'll unlock the secrets to achieving precise tightening and mitigating the risks associated with over-tightening or under-tightening.
Understanding Torque Wrenches
A torque wrench is an indispensable tool that allows users to tighten fasteners to a predetermined level of torque, typically measured in foot-pounds or newton-meters. This precise control over the tightening force is crucial in various applications, from automotive repairs to construction projects and manufacturing processes.
Types of Torque Wrenches | Description |
---|---|
Beam Wrenches | Employ a deflecting beam to indicate when the desired torque is reached. Known for durability and ease of use. |
Click Wrenches | Emit an audible click when the desired torque is reached. Provide auditory feedback for accurate tightening. |
Dial Wrenches | Feature a dial gauge that displays the torque value, providing a visual representation of the applied force. Highly accurate. |
Electronic Wrenches | Utilize digital displays for real-time torque readings, often with additional features like data logging and programmable settings. Offer unparalleled accuracy and versatility. |
Proper tightening is essential to prevent over-tightening, which can lead to damage or breakage of fasteners and components, as well as under-tightening, which can result in loosening and potential failure. By using a torque wrench, you can ensure that fasteners are tightened to the manufacturer's specifications, minimizing the risk of equipment failure or damage.
Consequences of Improper Tightening
Over-tightening:
Damage to fasteners or components
Warping or cracking of surrounding materials
Potential failure and safety hazards
Under-tightening:
Loosening of fasteners over time
Vibration and misalignment of components
Potential failure of systems or equipment
By using a torque wrench and adhering to the manufacturer's recommended torque specifications, you can prevent these issues and ensure that fasteners are tightened to the optimal level, maximizing the lifespan and performance of the components and systems involved.
Working Principle of Torque Wrenches
Torque wrenches are designed to measure the rotational force applied to a fastener, typically expressed in units of foot-pounds or newton-meters. The torque range and measurement scale of a wrench determine its suitability for specific applications, with some wrenches capable of measuring torque values from a few inch-pounds to several thousand foot-pounds.
Mechanism | Description |
---|---|
Click Mechanism | Produces an audible click when the set torque value is achieved, providing auditory feedback. |
Beam Deflection | A calibrated beam bends in proportion to the applied torque, allowing users to read the torque value on a scale. |
Digital Display | Advanced sensors and displays provide real-time torque readings, often with additional features like data logging and programmable settings. |
Regardless of the type, all torque wrenches rely on internal components such as springs, detents, and clutches to facilitate their operation. These components work together to disengage or indicate when the set torque value is reached, ensuring accurate and consistent torque application.
Measuring Rotational Force
At the core of a torque wrench's functionality is its ability to measure the rotational force applied to a fastener. This force, known as torque, is typically measured in units of foot-pounds or newton-meters, depending on the specific application and industry standards.
The torque range and measurement scale of a wrench determine its suitability for various tasks. For example, a wrench with a lower torque range may be suitable for delicate automotive repairs, while a higher-range wrench would be necessary for heavy-duty construction or industrial applications.
Internal Components and Their Roles
Component | Role |
---|---|
Springs | Store and release energy as torque is applied, allowing accurate measurement and indication of the applied force. |
Detents | Mechanical components that engage or disengage at specific torque values, enabling the click mechanism or beam deflection to occur. |
Clutches | Act as a safety mechanism to prevent over-tightening by disengaging when the desired torque is reached. |
By understanding the internal components and their roles, users can better appreciate the intricate engineering behind torque wrenches and the importance of proper maintenance and calibration to ensure accurate and reliable performance.
Accuracy and Calibration
Accurate torque readings are essential to ensure proper tightening and prevent potential failures or damage. Several factors can affect the accuracy of a torque wrench, including calibration, measurement scale, and usage technique.
Regular calibration is crucial to maintaining the accuracy of torque wrenches over time. Industry standards and guidelines typically recommend calibration intervals based on usage frequency and the specific application. Failure to calibrate a torque wrench can lead to inaccurate readings, potentially resulting in over-tightening or under-tightening of fasteners.
Calibration Process | Description |
---|---|
Specialized Equipment | Weights, calibration tools, and strict protocols are used to ensure precision and consistency. |
Measurement Range | The wrench is subjected to known torque values across its entire measurement range. |
Adjustments | Any deviations or discrepancies are noted, and adjustments are made to ensure accurate readings. |
It is important to note that calibration should be performed by trained professionals or authorized service centers to ensure the accuracy and reliability of the process.
Importance of Accurate Torque Readings
Accurate torque readings are paramount in various applications, from automotive repairs to construction projects and manufacturing processes. Inaccurate readings can lead to several issues, including:
Over-tightening
Damage to fasteners, components, or surrounding materials
Warping, cracking, or failure
Under-tightening
Loosening of fasteners over time
Vibration and misalignment of components
Potential failure of systems or equipment
Compromised performance and reliability
Safety hazards, particularly in critical applications
By ensuring accurate torque readings through regular calibration and proper usage techniques, users can mitigate these risks and maintain the integrity and longevity of the components and systems they work with.
Proper Usage Techniques
Proper usage techniques are essential to ensure accurate torque readings and prevent potential issues or damage. This includes setting the desired torque value correctly, applying force in the appropriate manner, and accounting for environmental factors that may impact torque readings.
Setting the Desired Torque Value
Before using a torque wrench, it is crucial to set the desired torque value according to the manufacturer's specifications or industry standards for the specific application. This may involve adjusting a dial, setting a micrometer, or programming the desired value into an electronic wrench.
Failure to set the correct torque value can lead to over-tightening or under-tightening of fasteners, potentially causing damage, component failure, or safety hazards.
Applying Force and Avoiding Jerky Movements
When using a torque wrench, it is important to apply force smoothly and consistently, avoiding jerky or sudden movements. Rapid or erratic force application can lead to inaccurate torque readings and potential damage to the wrench or the fastener being tightened.
Proper technique involves:
Applying force gradually and evenly
Using the wrench's handle as the primary point of application
Avoiding side-loading or applying force at an angle
Environmental Factors
Environmental factors such as temperature, lubrication, and fastener condition can impact torque readings and should be taken into consideration when using a torque wrench.
Factor | Impact |
---|---|
Temperature Variations | Can affect material properties, potentially altering the torque required for proper tightening. |
Lubrication | Presence or absence of lubricants can affect friction between the fastener and component, impacting torque readings. |
Fastener Condition | Worn or damaged threads may require different torque values or special considerations to ensure proper tightening and prevent further damage. |
By accounting for these environmental factors and adjusting usage techniques accordingly, users can maximize the accuracy and reliability of their torque wrenches, ensuring optimal performance and minimizing the risk of potential issues or failures.
Maintenance and Storage
Proper maintenance and storage practices are essential to ensure the longevity and accuracy of torque wrenches. Regular cleaning, lubrication, and adherence to recommended storage conditions can help prevent premature wear, corrosion, and potential damage to these precision tools.
Cleaning and Lubrication
Regular cleaning removes dirt, debris, and contaminants that can accumulate on the wrench's surface and internal components.
Lubrication ensures smooth operation and prevents premature wear or corrosion.
Manufacturers typically recommend specific lubricants and application procedures.
Proper Storage Conditions
Store wrenches in a clean, dry environment, away from extreme temperatures, moisture, and direct sunlight.
Use protective cases or pouches when not in use to prevent accidental damage or exposure to contaminants.
Avoiding Misuse
It is important to avoid misusing torque wrenches as breaker bars or for purposes other than their intended use. Torque wrenches are precision instruments designed to measure and apply specific torque values, and using them for tasks such as loosening or breaking fasteners can damage their internal components and compromise their accuracy.
If a fastener is stuck or requires excessive force to loosen, it is recommended to use appropriate tools, such as breaker bars or impact wrenches, rather than risking damage to the torque wrench.
By following proper maintenance and storage practices, and avoiding misuse, users can extend the lifespan of their torque wrenches and ensure accurate and reliable performance over time.
Conclusion
Torque wrenches are essential tools for achieving precise tightening of fasteners, ensuring optimal performance, and preventing potential failures or damage in various applications. By understanding the different types, working principles, calibration requirements, and proper usage techniques, users can maximize the accuracy and longevity of these invaluable tools.
Regular maintenance, adherence to manufacturer instructions, and seeking professional calibration services when necessary are key to maintaining the reliability of torque wrenches across automotive repairs, construction projects, and manufacturing processes. With the knowledge gained from this comprehensive guide, you can confidently apply the right torque, every time, and safeguard the integrity of your components and systems.
FAQs
What is the purpose of a torque wrench?
A torque wrench is designed to apply a precise rotational force (torque) to fasteners like nuts and bolts. It prevents over-tightening or under-tightening, which can lead to component failure or damage.
How does a torque wrench indicate when the desired torque is reached?
Different torque wrenches use various mechanisms like an audible click, a deflecting beam, or a digital display to indicate when the set torque value is achieved.
What are the consequences of improper tightening?
Over-tightening can damage fasteners, components, or surrounding materials, while under-tightening can cause loosening, vibration, misalignment, and potential failure of systems or equipment.
What internal components enable a torque wrench to measure rotational force?
Springs, detents, and clutches work together to store and release energy, engage or disengage at specific torque values, and prevent over-tightening.
Why is regular calibration important for torque wrenches?
Regular calibration ensures accurate torque readings over time, as factors like usage frequency and environmental conditions can affect the wrench's accuracy.
How can environmental factors impact torque readings?
Temperature variations, lubrication presence or absence, and fastener condition can influence the torque required for proper tightening and affect the wrench's readings.
What is the recommended technique for applying force with a torque wrench?
Force should be applied gradually, evenly, and using the wrench's handle as the primary point of application, avoiding jerky movements or side-loading.
How can misuse affect a torque wrench's performance?
Using a torque wrench as a breaker bar or for purposes other than its intended use can damage its internal components and compromise its accuracy.
What are the recommended storage conditions for torque wrenches?
Torque wrenches should be stored in a clean, dry environment, away from extreme temperatures, moisture, and direct sunlight, and protected in cases or pouches.
When should a professional calibration service be sought?
If there are serious doubts about the ability to calibrate the torque wrench accurately at home, it is recommended to seek professional calibration services.
Bình luận (0)
Bài viết đề xuất
Choosing the right braking system for your bicycle can significantly impact your riding experience, safety, and overall performance. In this comprehensive guide, we'll delve into the intricate details of two popular rim brake options – v-brakes and cantilever brakes – to help you make an informed decision based on your specific cycling needs.
Shock absorbers play a vital role in ensuring a smooth, controlled, and safe driving experience. As an integral part of a vehicle's suspension system, they work in tandem with the springs to dampen the impact of bumps and irregularities on the road, maintaining optimal tire-to-road contact and handling.
Brake fluid is a hydraulic fluid used in brake and clutch systems of vehicles. It typically contains toxic alcohols like ethylene glycol and diethylene glycol (DEG). Ingestion of brake fluid, whether accidental or intentional, can lead to poisoning with potentially life-threatening consequences.
Bài viết liên quan
Socket wrench sets are versatile and indispensable tools for anyone working with nuts, bolts, and fasteners. Whether you're a professional mechanic, a skilled tradesperson, or a DIY enthusiast, mastering the use of these essential tools will streamline your projects and ensure efficient, safe, and precise results.
Maintaining your vehicle's engine is crucial for ensuring its longevity and optimal performance. One of the most essential maintenance tasks is regularly changing the oil filter, which traps contaminants and prevents them from circulating through the engine.
Maintaining your vehicle's engine in top condition is crucial for ensuring optimal performance, fuel efficiency, and longevity. One of the most critical components in a gasoline-powered engine is the spark plug, responsible for igniting the air-fuel mixture and enabling combustion.