A serpentine belt, also known as a multi-rib or poly-v belt, is a crucial component in modern automotive engines. This single, continuous belt is responsible for driving multiple accessories simultaneously, following a winding path around various pulleys. By efficiently transmitting power from the engine's crankshaft, the serpentine belt keeps vital components such as the alternator, power steering pump, air conditioning compressor, and water pump running smoothly.
Material Innovations for Brake Pads and Rotors (Improved Performance, Durability)

Material Innovations for Brake Pads and Rotors (Improved Performance, Durability)
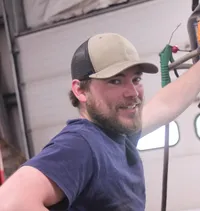
In the world of automotive safety and performance, brake pads and rotors play a crucial role in ensuring that vehicles can stop effectively and reliably. However, traditional brake materials have limitations that can affect braking performance, durability, and overall safety. To address these challenges, researchers and manufacturers have been developing innovative materials for brake pads and rotors that offer improved performance, longer life spans, and enhanced safety features. This article will explore the latest advancements in brake pad and rotor materials, including advanced composites, innovative alloys, coatings, and surface treatments, as well as nanoparticle reinforcements and adaptive materials. We will also discuss the environmental considerations and future trends in brake material technology.
I. Introduction
Brake pads and rotors are critical components of a vehicle's braking system, responsible for converting kinetic energy into heat through friction to slow down or stop the vehicle. The performance and durability of these components directly impact the safety of the vehicle and its occupants. Traditional brake materials, such as organic or semi-metallic brake pads and cast iron rotors, have been used for decades. However, these materials have limitations in terms of wear resistance, heat dissipation, and noise reduction, which can compromise braking performance and safety.
To overcome these limitations, researchers and manufacturers have been developing advanced materials for brake pads and rotors that offer superior properties and performance characteristics. These innovations include the use of ceramic matrix composites, metal matrix composites, and carbon-carbon composites for brake pads, as well as lightweight alloys and high-strength materials for brake rotors. Additionally, coatings and surface treatments, nanoparticle reinforcements, and adaptive materials are being explored to further enhance the performance and durability of brake components.
II. Advanced Composite Materials for Brake Pads
Composite materials have emerged as a promising solution for brake pad applications, offering a combination of high performance, durability, and reduced environmental impact. These materials typically consist of a matrix (e.g., ceramic, metal, or polymer) reinforced with fibers or particles to achieve desired properties.
Composite Material | Matrix | Reinforcement | Key Benefits |
---|---|---|---|
Ceramic Matrix Composites (CMCs) | Ceramic | Ceramic fibers or particles | High temperature stability, wear resistance, lightweight |
Metal Matrix Composites (MMCs) | Metal (e.g., aluminum, titanium, copper) | Ceramic particles or fibers | High thermal conductivity, wear resistance, tailorable properties |
Carbon-Carbon Composites (CCCs) | Carbon | Carbon fibers | Exceptional high-temperature performance, lightweight, high specific heat capacity |
A. Ceramic Matrix Composites
Ceramic matrix composites (CMCs) are a class of materials that consist of a ceramic matrix reinforced with ceramic fibers or particles. These materials offer several advantages for brake pad applications, including:
High temperature stability: CMCs can withstand extreme temperatures generated during braking without significant degradation or loss of performance.
Wear resistance: The hard ceramic matrix and reinforcements provide excellent wear resistance, extending the life of the brake pads.
Lightweight: CMCs are typically lighter than traditional metallic brake pads, reducing unsprung weight and improving vehicle handling.
B. Metal Matrix Composites
Metal matrix composites (MMCs) are another class of materials that have shown promise for brake pad applications. These materials consist of a metallic matrix (e.g., aluminum, titanium, or copper) reinforced with ceramic particles or fibers. MMCs offer several advantages over traditional brake pad materials, including:
High thermal conductivity: The metallic matrix allows for efficient heat dissipation, reducing brake fade and improving performance.
Wear resistance: The ceramic reinforcements provide enhanced wear resistance, extending the life of the brake pads.
Tailorable properties: The composition and processing of MMCs can be optimized to achieve specific performance characteristics, such as friction coefficient or noise reduction.
C. Carbon-Carbon Composites
Carbon-carbon composites (CCCs) are a unique class of materials that consist of a carbon matrix reinforced with carbon fibers. These materials have found application in high-performance braking systems, particularly in motorsports and aerospace industries. CCCs offer several advantages, including:
Exceptional high-temperature performance: CCCs can maintain their mechanical properties and friction characteristics at temperatures exceeding 1,000°C.
Lightweight: CCCs have a low density compared to metallic brake materials, reducing unsprung weight and improving vehicle dynamics.
High specific heat capacity: The high specific heat capacity of CCCs allows for efficient energy absorption during braking, reducing brake fade.
III. Innovative Alloys for Brake Rotors
In addition to advancements in brake pad materials, researchers and manufacturers have been developing innovative alloys for brake rotors to improve performance, durability, and safety. These alloys aim to address the limitations of traditional cast iron rotors, such as excessive weight, thermal fatigue, and corrosion.
Alloy | Key Benefits |
---|---|
Aluminum-Beryllium (Al-Be) | Lightweight, high specific heat capacity, wear resistance |
Titanium | High strength-to-weight ratio, thermal stability, corrosion resistance |
High-Strength Cast Iron | Increased tensile strength, improved thermal conductivity, enhanced wear resistance |
A. Aluminum-Beryllium Alloys
Aluminum-beryllium (Al-Be) alloys have been explored as a lightweight alternative to cast iron for brake rotors. These alloys offer several advantages, including:
Lightweight: Al-Be alloys have a density that is approximately 70% lower than cast iron, significantly reducing unsprung weight and improving vehicle handling.
High specific heat capacity: The high specific heat capacity of Al-Be alloys allows for efficient heat dissipation during braking, reducing brake fade and improving performance.
Wear resistance: The addition of beryllium to the aluminum matrix enhances the wear resistance of the alloy, extending the life of the brake rotors.
B. Titanium Alloys
Titanium alloys have also been investigated for brake rotor applications, particularly in high-performance vehicles and motorsports. These alloys offer several advantages, including:
High strength-to-weight ratio: Titanium alloys have a high strength-to-weight ratio, allowing for the design of lightweight and durable brake rotors.
Thermal stability: Titanium alloys maintain their mechanical properties at elevated temperatures, reducing the risk of thermal fatigue and warping.
Corrosion resistance: Titanium alloys exhibit excellent corrosion resistance, maintaining their performance and appearance over time.
C. High-Strength Cast Iron
While cast iron has been the traditional material for brake rotors, advancements in casting techniques and alloy compositions have led to the development of high-strength cast iron rotors. These rotors offer improved mechanical properties and durability compared to conventional cast iron rotors. Some of the advantages of high-strength cast iron rotors include:
Increased tensile strength: High-strength cast iron rotors have higher tensile strength than conventional cast iron, reducing the risk of cracking and failure under high-stress conditions.
Improved thermal conductivity: The optimized microstructure and composition of high-strength cast iron rotors allow for better heat dissipation, reducing thermal fatigue and warping.
Enhanced wear resistance: The improved mechanical properties of high-strength cast iron rotors result in better wear resistance, extending the life of the rotors.
IV. Coatings and Surface Treatments
Coatings and surface treatments have been developed to enhance the performance and durability of brake pads and rotors. These treatments aim to address specific issues, such as corrosion, wear, and thermal management.
A. Thermal Barrier Coatings
Thermal barrier coatings (TBCs) are ceramic coatings applied to the surface of brake rotors to improve their thermal management properties. TBCs offer several advantages, including:
Insulating properties: TBCs act as a thermal insulator, reducing the amount of heat transferred from the rotor to the surrounding components, such as the brake caliper and wheel bearings.
Temperature reduction: By reducing heat transfer, TBCs help to lower the overall temperature of the braking system, improving performance and reducing the risk of brake fade.
Extended component life: The reduced thermal stress on surrounding components can extend their life, reducing maintenance costs and improving overall vehicle reliability.
B. Wear-Resistant Coatings
Wear-resistant coatings, such as hard ceramic or diamond-like carbon (DLC) coatings, can be applied to brake pads and rotors to improve their wear resistance and extend their life. These coatings offer several advantages, including:
Hard, abrasion-resistant surface: Wear-resistant coatings provide a hard, abrasion-resistant surface that reduces wear rates and extends the life of brake components.
Reduced brake dust: The improved wear resistance of coated brake pads and rotors can lead to a reduction in brake dust generation, improving air quality and reducing the environmental impact of braking.
Consistent friction performance: Wear-resistant coatings can help to maintain a consistent friction coefficient over the life of the brake components, ensuring reliable and predictable braking performance.
C. Corrosion-Resistant Coatings
Corrosion-resistant coatings, such as zinc or nickel-based coatings, can be applied to brake rotors to protect them from environmental factors that can lead to corrosion and degradation. These coatings offer several advantages, including:
Protection against salt, moisture, and other corrosive agents: Corrosion-resistant coatings act as a barrier, preventing corrosive agents from attacking the underlying metal surface.
Maintained performance and appearance: By preventing corrosion, these coatings help to maintain the performance and appearance of brake rotors over time, reducing the need for frequent replacement.
Extended rotor life: Corrosion-resistant coatings can significantly extend the life of brake rotors, reducing maintenance costs and improving vehicle reliability.
V. Nanoparticle Reinforcements and Friction Modifiers
Nanoparticle reinforcements and friction modifiers have been explored as a means to enhance the performance and durability of brake pads. These additives can be incorporated into the brake pad material to improve specific properties, such as friction stability, wear resistance, and thermal conductivity.
A. Silica Nanoparticles
Silica nanoparticles have been investigated as a reinforcement for brake pad materials, offering several advantages, including:
Enhanced friction stability: The addition of silica nanoparticles to brake pad materials can help to stabilize the friction coefficient over a wide range of temperatures and operating conditions, ensuring consistent braking performance.
Improved wear resistance: Silica nanoparticles can increase the hardness and wear resistance of brake pad materials, extending their life and reducing the generation of brake dust.
Increased thermal conductivity: The incorporation of silica nanoparticles can improve the thermal conductivity of brake pad materials, allowing for better heat dissipation and reducing the risk of brake fade.
B. Graphite Lubricants and Ceramic Friction Modifiers
Graphite lubricants and ceramic friction modifiers can be added to brake pad materials to improve their friction and wear characteristics. These additives offer several advantages, including:
Reduced wear and noise: Graphite lubricants act as solid lubricants, reducing wear and noise generation during braking.
Stable friction performance: Ceramic friction modifiers can help to maintain a stable friction coefficient across a wide range of temperatures, ensuring consistent braking performance.
Improved fade resistance: The addition of ceramic friction modifiers can increase the thermal stability of brake pad materials, reducing the risk of brake fade under high-temperature conditions.
VI. Fiber Reinforcements
Fiber reinforcements have been used to enhance the mechanical properties and performance of brake pad materials. These reinforcements can be in the form of organic or inorganic fibers, each offering unique advantages.
A. Kevlar and Aramid Fibers
Kevlar and aramid fibers are high-strength, heat-resistant organic fibers that can be incorporated into brake pad materials to improve their performance. These fibers offer several advantages, including:
High strength and thermal stability: Kevlar and aramid fibers have high tensile strength and can maintain their mechanical properties at elevated temperatures, improving the overall strength and fade resistance of brake pads.
Improved wear resistance: The incorporation of these fibers can increase the wear resistance of brake pad materials, extending their life and reducing the generation of brake dust.
Reduced noise and vibration: The damping properties of Kevlar and aramid fibers can help to reduce noise and vibration during braking, improving driver comfort and reducing the risk of brake squeal.
B. Basalt Fibers
Basalt fibers are natural mineral fibers that have been explored as a cost-effective and environmentally friendly reinforcement for brake pad materials. These fibers offer several advantages, including:
High temperature resistance: Basalt fibers can withstand temperatures up to 1,200°C, making them suitable for use in high-temperature braking applications.
Good mechanical properties: Basalt fibers have high tensile strength and modulus, improving the overall strength and stiffness of brake pad materials.
Eco-friendly and cost-effective: As a natural mineral fiber, basalt is an eco-friendly and cost-effective alternative to synthetic fibers, such as glass or carbon fibers.
VII. Adaptive and Smart Materials
Adaptive and smart materials have been investigated for their potential to enhance the performance and functionality of brake pads and rotors. These materials can respond to changes in their environment or be actively controlled to optimize braking performance.
A. Piezoelectric Materials
Piezoelectric materials, such as lead zirconate titanate (PZT), can be integrated into brake pads or rotors to provide active vibration control and noise reduction. These materials offer several advantages, including:
Active vibration control: Piezoelectric materials can convert mechanical energy (vibrations) into electrical energy, which can be dissipated or used to counteract the vibrations, reducing brake noise and improving driver comfort.
Sensor integration: Piezoelectric materials can also be used as sensors to monitor the condition of brake components, such as wear, temperature, or pressure, enabling predictive maintenance and improving vehicle safety.
Compact and lightweight: Piezoelectric materials are compact and lightweight, making them suitable for integration into brake components without significantly increasing their size or weight.
B. Shape Memory Alloys
Shape memory alloys (SMAs), such as nickel-titanium (NiTi), have been explored for their potential to enable adaptive brake pad and rotor designs. These materials offer unique properties, including:
Temperature-dependent shape change: SMAs can be programmed to change shape at specific temperatures, allowing for the design of brake components that adapt to different operating conditions.
Superelastic behavior: SMAs exhibit superelastic behavior, meaning they can undergo large deformations and return to their original shape when the load is removed, potentially enabling the design of more resilient brake components.
Vibration damping: The hysteretic behavior of SMAs can provide inherent vibration damping, reducing brake noise and improving driver comfort.
VIII. Environmental Considerations and Sustainability
As the automotive industry moves towards more sustainable and environmentally friendly practices, the development of brake pad and rotor materials must also consider their environmental impact and sustainability.
A. Eco-Friendly Material Alternatives
Researchers and manufacturers are exploring eco-friendly material alternatives for brake pads and rotors, such as:
Bio-derived materials: Natural fibers, such as hemp, flax, or sisal, can be used as reinforcements in brake pad materials, reducing the reliance on synthetic fibers and improving the biodegradability of the pads.
Recycled materials: The use of recycled materials, such as recycled metal fibers or recycled polymer resins, can reduce the environmental impact of brake component production and promote a circular economy.
Low-emission materials: The development of brake pad materials with reduced levels of heavy metals, such as copper or antimony, can help to minimize the environmental impact of brake wear particles and comply with increasingly stringent regulations.
B. Brake Dust Reduction Strategies
Brake dust, which is generated by the wear of brake pads and rotors, has been identified as a significant source of particulate matter emissions from vehicles. To address this issue, several strategies have been developed, including:
Dust collection and filtration systems: The integration of dust collection and filtration systems into the brake caliper or wheel assembly can help to capture and contain brake wear particles, reducing their release into the environment.
Optimized pad and rotor materials: The development of brake pad and rotor materials with improved wear resistance and reduced dust generation can help to minimize the environmental impact of brake wear particles.
Regenerative braking: The use of regenerative braking systems in electric and hybrid vehicles can reduce the reliance on friction brakes, thereby reducing brake wear and dust generation.
IX. Testing, Validation, and Future Developments
To ensure the safety, performance, and reliability of new brake pad and rotor materials, rigorous testing and validation processes are required. Additionally, ongoing research and development efforts are essential to address emerging challenges and opportunities in brake technology.
A. Advanced Testing Methods for Brake Materials
Advanced testing methods are being developed to accurately assess the performance and durability of brake materials under various operating conditions. These methods include:
Simulation-based testing: Finite element analysis (FEA) and computational fluid dynamics (CFD) simulations can be used to predict the thermal, mechanical, and tribological behavior of brake materials, reducing the need for extensive physical testing.
Real-world performance evaluation: The use of instrumented vehicles and data acquisition systems can provide valuable insights into the real-world performance of brake materials, enabling the optimization of material compositions and designs.
Accelerated life testing: Accelerated life testing methods, such as high-temperature or high-load testing, can be used to assess the long-term durability of brake materials in a shorter timeframe.
B. Emerging Trends and Research Directions
As the automotive industry continues to evolve, several emerging trends and research directions are shaping the future of brake material technology. These include:
Integration of sensor technologies: The integration of sensors, such as wear sensors, temperature sensors, or pressure sensors, into brake pads and rotors can enable real-time monitoring of brake performance and condition, facilitating predictive maintenance and improving vehicle safety.
Multifunctional materials: The development of multifunctional brake materials that combine multiple desirable properties, such as high friction, low wear, and low noise, can help to optimize brake performance and reduce the need for complex multi-material designs.
Self-healing materials: The exploration of self-healing materials, such as polymers or composites with the ability to autonomously repair minor damage or cracks, can potentially extend the life of brake components and improve their reliability.
Nanomaterial-based friction modifiers: The use of nanomaterials, such as graphene or carbon nanotubes, as friction modifiers in brake pad materials can help to enhance their tribological properties and reduce wear and noise.
Intelligent brake systems: The development of intelligent brake systems that can adapt to different driving conditions, vehicle loads, or driver preferences can optimize braking performance, improve safety, and enhance the overall driving experience.
X. Conclusion
The development of innovative brake pad and rotor materials has the potential to significantly improve vehicle safety, performance, and sustainability. By leveraging advanced composites, alloys, coatings, and adaptive materials, researchers and manufacturers are addressing the limitations of traditional brake materials and pushing the boundaries of brake technology.
As the automotive industry continues to evolve, the integration of sensor technologies, multifunctional materials, and intelligent brake systems will play a crucial role in shaping the future of braking. However, the successful implementation of these innovations will require close collaboration between material scientists, engineers, and industry stakeholders to ensure their safety, reliability, and cost-effectiveness.
Ongoing research and development efforts in brake material technology will not only enhance vehicle performance and safety but also contribute to the broader goals of environmental sustainability and reduced transportation-related emissions. As stricter regulations and consumer demands drive the push for cleaner, safer, and more efficient vehicles, the continued advancement of brake pad and rotor materials will be essential in meeting these challenges and paving the way for a more sustainable future in transportation.
In summary, the key points covered in this article include:
The limitations of traditional brake materials and the need for innovative solutions
Advanced composite materials for brake pads, such as ceramic matrix composites, metal matrix composites, and carbon-carbon composites
Innovative alloys for brake rotors, including aluminum-beryllium alloys, titanium alloys, and high-strength cast iron
Coatings and surface treatments for improved thermal management, wear resistance, and corrosion resistance
Nanoparticle reinforcements and friction modifiers for enhanced performance and durability
Fiber reinforcements, such as Kevlar, aramid, and basalt fibers, for improved mechanical properties and performance
Adaptive and smart materials, including piezoelectric materials and shape memory alloys, for active vibration control and adaptive designs
Environmental considerations and sustainability, focusing on eco-friendly material alternatives and brake dust reduction strategies
Advanced testing methods and emerging trends in brake material technology, such as sensor integration, multifunctional materials, and intelligent brake systems
As the automotive industry continues to evolve and innovate, the development of advanced brake pad and rotor materials will remain a critical area of research and development. By addressing the challenges associated with traditional brake materials and leveraging cutting-edge technologies, researchers and manufacturers can create safer, more efficient, and more sustainable braking systems for the vehicles of the future.
FAQs
What are the environmental impacts of different brake pad materials?
Organic brake pads are the most eco-friendly option as they produce less dust and are made from natural materials. Metallic and ceramic pads can generate more brake dust which contributes to airborne particulates.
How do brake pad materials affect noise levels during braking?
Organic brake pads are typically the quietest option due to their softer composition. Metallic pads tend to be the noisiest, while ceramic pads offer a balance of quiet operation and performance.
What is the typical lifespan of each type of brake pad material?
Ceramic brake pads generally last the longest, followed by metallic pads. Organic pads usually have the shortest lifespan due to their softer friction material.
Are there any brake pad materials that are better suited for electric vehicles?
Ceramic brake pads are a good choice for electric vehicles as they produce less dust, handle heat well, and provide consistent performance. Some manufacturers also offer EV-specific brake pad compounds optimized for regenerative braking systems.
How do different brake pad materials affect rotor wear?
Metallic brake pads tend to cause the most wear on rotors due to their abrasive nature. Ceramic and organic pads are gentler on rotors, with ceramic pads offering the least amount of rotor wear.
Can brake pad materials be mixed and matched on the same vehicle?
While it is possible to use different brake pad materials on the front and rear axles, it is generally recommended to use the same material on all four wheels for balanced braking performance. Mixing pad types can lead to uneven wear and unpredictable braking characteristics.
Are there any brake pad materials that perform better in wet conditions?
Sintered metallic brake pads are known for their superior performance in wet and muddy conditions due to their porous structure. Organic and ceramic pads may experience reduced performance in wet weather.
How do brake pad materials affect heat dissipation and brake fade?
Metallic brake pads are excellent at dissipating heat, reducing the risk of brake fade during heavy use. Ceramic pads also handle heat well, while organic pads are more susceptible to fade at high temperatures.
Are there any specific break-in procedures for different brake pad materials?
All new brake pads require a break-in period to ensure optimal performance and longevity. The specific procedure may vary slightly depending on the manufacturer's recommendations, but generally involves a series of moderate to hard stops to properly seat the pads against the rotors.
Can brake pad materials be recycled or disposed of in an eco-friendly manner?
Most brake pad materials can be recycled through specialized facilities. It is important to properly dispose of worn brake pads as they may contain heavy metals and other pollutants that can harm the environment if not handled correctly.
Bình luận (0)
Bài viết đề xuất
Maintaining your 6.7L Cummins diesel engine is a crucial aspect of ensuring optimal performance, fuel efficiency, and longevity.
The powertrain control module (PCM), also known as an engine control module (ECM) or engine control unit (ECU), is the brain of your vehicle's engine management system. This sophisticated computer oversees a wide range of critical functions, from fuel injection and ignition timing to emissions control and transmission shifting. When the PCM begins to fail, it can trigger a variety of drivability issues that may leave you stranded on the side of the road.
The fuel pressure regulator is a crucial component in modern fuel injection systems, responsible for maintaining the correct fuel pressure within the fuel rail.