Condensers are a crucial component of air conditioning and refrigeration systems, responsible for dissipating heat from the refrigerant. They play a vital role in the overall efficiency and performance of these systems.
Air in the Refrigerant Circuit: Causes, Effects, and Solutions
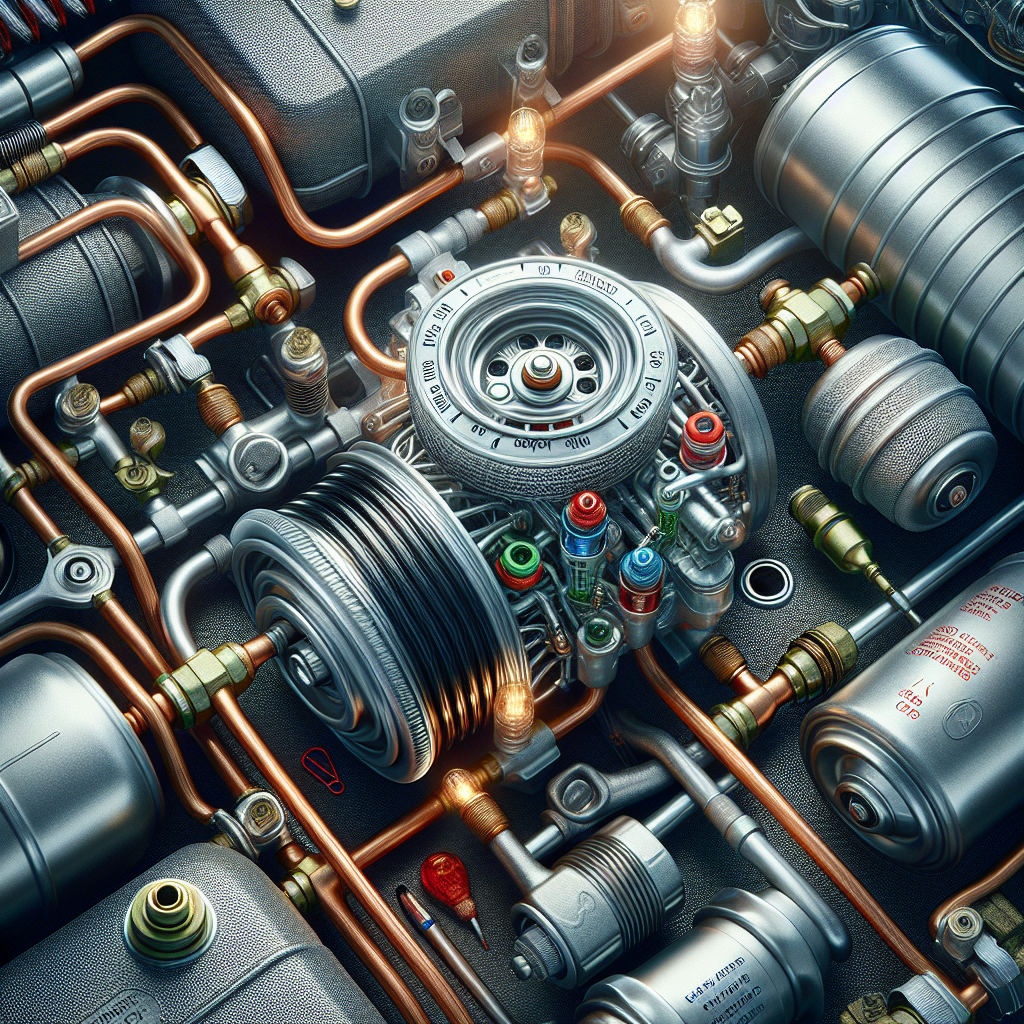
Air in the Refrigerant Circuit: Causes, Effects, and Solutions
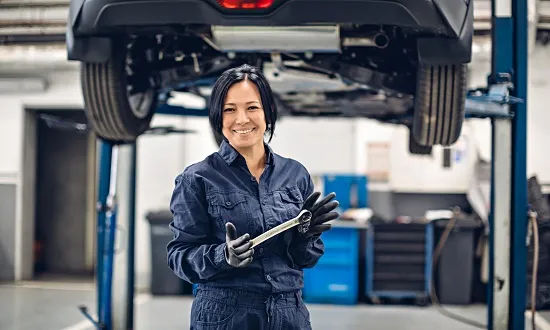
The refrigerant circuit is the heart of any cooling system, be it an air conditioner, refrigerator, or industrial chiller. While designed as a sealed system, air can sometimes infiltrate the refrigerant circuit, leading to reduced efficiency, increased wear, and potential system failure. This comprehensive article delves into the causes, effects, identification methods, and solutions for dealing with air contamination in the refrigerant circuit, ensuring your cooling system operates at peak performance.
Understanding the Refrigerant Circuit
The refrigerant circuit is a closed-loop system that facilitates heat transfer through the phase changes of the refrigerant. It comprises four main components:
Component | Function |
---|---|
Compressor | Circulates the refrigerant and maintains pressure differential |
Condenser | Releases heat from the refrigerant, causing condensation |
Expansion Valve | Regulates refrigerant flow, allowing expansion and cooling |
Evaporator | Absorbs heat from the surrounding environment, causing evaporation |
The compressor is the heart of the circuit, responsible for circulating the refrigerant. The condenser and evaporator facilitate the condensation and evaporation processes, respectively, while the expansion valve regulates the refrigerant flow, enabling the phase changes necessary for heat transfer.
The refrigerant circuit is designed as a closed-loop, sealed system to maintain optimal performance and efficiency. Any breach in the system's integrity can allow air or other contaminants to enter, disrupting the delicate balance of the refrigerant cycle and compromising the system's ability to transfer heat effectively.
Causes of Air Entry into the Refrigerant Circuit
Air can infiltrate the refrigerant circuit through various pathways, each with its own set of contributing factors. Understanding these causes is crucial for preventing and addressing air contamination.
Leaks in the System
One of the primary causes of air entry is leaks in the refrigerant circuit components or connections. These leaks can occur due to various reasons:
Improper installation or maintenance practices
Corrosion or wear of components over time
Physical damage to refrigerant lines or components
Even the smallest crack or loose connection can allow air to seep into the system, compromising its performance and efficiency.
Improper Evacuation Procedures
During installation, repair, or maintenance, the refrigerant circuit must be properly evacuated using a vacuum pump to remove any residual air or non-condensable gases. Failure to follow proper evacuation procedures can leave behind traces of air, which can accumulate over time and cause issues.
Chemical Reactions within the System
In some cases, chemical reactions within the refrigerant circuit can produce non-condensable gases, which behave similarly to air. These gases can arise from various factors:
Incompatible materials
Moisture ingress
Refrigerant breakdown due to excessive temperatures or pressures
Effects of Air in the Refrigerant Circuit
The presence of air in the refrigerant circuit can have far-reaching consequences, impacting the system's performance, efficiency, and longevity.
Reduced Cooling Capacity and Efficiency
Air acts as an insulator, hindering the heat transfer process and reducing the system's ability to cool effectively. This results in decreased cooling capacity and lower overall efficiency, leading to higher energy consumption and increased operating costs.
To illustrate the impact of air on cooling capacity, consider the following example:
Air Percentage | Cooling Capacity Reduction |
---|---|
1% | 3-5% |
5% | 15-20% |
10% | 30-40% |
As the table shows, even a small amount of air can significantly reduce the cooling capacity of the system, highlighting the importance of maintaining a sealed and air-free refrigerant circuit.
Increased Compressor Discharge Temperatures
Air increases the compressor's workload, as it must work harder to circulate the refrigerant and maintain the necessary pressure differential. This increased workload leads to higher discharge temperatures, which can cause premature wear and damage to the compressor over time.
The relationship between air presence and compressor discharge temperature can be seen in the following table:
Air Percentage | Discharge Temperature Increase |
---|---|
1% | 5-10°F |
5% | 25-50°F |
10% | 50-100°F |
As the table illustrates, even a small amount of air can significantly increase the compressor's discharge temperature, leading to potential overheating and damage.
Increased Condensing Pressures
Non-condensable gases, including air, tend to accumulate in the condenser, increasing the condensing pressure and putting additional strain on the system. This can lead to reduced heat rejection efficiency and further compromise the system's overall performance.
Potential for Compressor Damage or Failure
In extreme cases, excessive air in the refrigerant circuit can cause the compressor to overheat, leading to premature failure or even complete breakdown. This can result in costly repairs or the need for a complete system replacement.
Common signs of compressor damage due to air contamination include:
Abnormal noise or vibration
Excessive oil consumption
Reduced cooling capacity
Complete failure to start or run
Identifying Air in the Refrigerant Circuit
Early detection of air contamination is crucial for preventing further damage and addressing the issue promptly. There are several methods for identifying the presence of air in the refrigerant circuit.
Observing Symptoms
One of the first indicators of air in the system is the presence of unusual symptoms, such as:
Frosting or sweating on refrigerant lines or components
Unusual noises from the compressor
High head pressures on the system gauges
These symptoms can be early warning signs of air contamination and should be investigated further.
Sight Glass Inspection
Many refrigerant circuits are equipped with sight glasses or moisture indicators, which can reveal the presence of air bubbles or non-condensable gases. Regular inspection of these components can help identify air infiltration before it becomes a more significant issue.
The following table outlines the typical appearance of sight glasses with varying levels of air contamination:
Air Contamination Level | Sight Glass Appearance |
---|---|
None | Clear liquid refrigerant flow |
Low | Small air bubbles or foam |
Moderate | Larger air bubbles or foam |
High | Continuous stream of air bubbles or foam |
Non-Condensable Gas Measurement
Specialized tools, such as non-condensable gas detectors, can measure the levels of non-condensable gases in the system, including air. These tools provide a quantitative assessment of the air contamination, allowing for more accurate diagnosis and treatment.
Removing Air from the Refrigerant Circuit
Once air contamination has been identified, it is crucial to take immediate action to remove the air from the refrigerant circuit and restore the system's efficiency and performance.
Proper Evacuation Procedures
The most effective way to remove air from the refrigerant circuit is through proper evacuation procedures using a vacuum pump. This process involves:
Connecting the vacuum pump to the system's service ports
Evacuating the system to remove air and non-condensable gases
Following the manufacturer's recommended evacuation procedures and guidelines
Proper evacuation ensures that the system is free of air and other contaminants, allowing it to operate at peak efficiency.
The evacuation process typically follows these steps:
Connect the vacuum pump to the system's service ports
Evacuate the system to a specific vacuum level (e.g., 500 microns or lower)
Isolate the vacuum pump and monitor the system for any pressure rise (indicating a leak)
If no leaks are detected, proceed with charging the system with refrigerant
Purging Non-Condensable Gases
In some cases, purging the system may be necessary to remove non-condensable gases, including air. This process involves:
Identifying and accessing the purge valve or service port
Allowing the non-condensable gases to escape through the purge valve
Monitoring the system's pressures and temperatures during the purging process
Purging can be an effective method for removing stubborn air pockets or accumulated non-condensable gases.
Leak Testing and Repair
After removing the air from the system, it is essential to identify and repair any leaks that may have allowed air to enter in the first place. Leak testing can be performed using various methods:
Pressure testing with nitrogen or another inert gas
Electronic leak detectors
Visual inspections for signs of damage or wear
Common leak testing methods include:
Method | Description |
---|---|
Pressure Testing | The system is pressurized with an inert gas, and any pressure drop is monitored to detect leaks. |
Electronic Leak Detectors | Handheld devices that can detect refrigerant leaks by sensing the presence of halogen gases. |
Visual Inspection | A thorough visual examination of the system components and connections for signs of damage or wear. |
Once the leaks have been identified and repaired, the system can be properly evacuated and recharged with the appropriate refrigerant, ensuring optimal performance and preventing future air contamination.
Preventing Air Entry into the Refrigerant Circuit
While removing air from the refrigerant circuit is essential, preventing its entry in the first place is even more critical. Several best practices can be followed to minimize the risk of air contamination.
Proper Installation and Maintenance Practices
Following the manufacturer's guidelines for installation, repair, and maintenance is crucial to ensuring the integrity of the refrigerant circuit. This includes:
Proper brazing and leak testing techniques
Adherence to evacuation and charging procedures
Regular inspections and preventive maintenance
Trained and certified technicians should always perform these tasks to ensure they are carried out correctly and to industry standards.
Use of High-Quality Components and Materials
Investing in high-quality components and materials can significantly reduce the risk of leaks and failures that can lead to air entry. This includes:
Using refrigerant-grade copper tubing and fittings
Selecting components from reputable manufacturers
Ensuring compatibility between system components and refrigerants
High-quality components are less prone to corrosion, wear, and damage, reducing the likelihood of air infiltration over time.
Regular System Inspections and Monitoring
Conducting regular inspections and monitoring of the refrigerant circuit can help identify potential issues before they escalate. This includes:
Visual inspections for signs of wear, damage, or leaks
Monitoring system pressures and temperatures
Checking sight glasses or moisture indicators
Regular inspections and monitoring can catch air contamination early, allowing for prompt action and minimizing the risk of further damage or system failure.
Recommended inspection and monitoring practices include:
Monthly visual inspections
Quarterly system pressure and temperature checks
Annual comprehensive system evaluation
Conclusion
Air contamination in the refrigerant circuit can have severe consequences for the performance, efficiency, and longevity of any cooling system. By understanding the causes, effects, identification methods, and solutions outlined in this article, you can take proactive measures to prevent air entry and address any existing air contamination promptly.
Remember, a well-maintained and properly sealed refrigerant circuit is essential for ensuring your cooling system operates at peak performance, minimizing energy consumption, and prolonging its lifespan. Regular inspections, adherence to best practices, and the use of high-quality components can go a long way in preventing air-related issues and ensuring the reliable operation of your cooling system.
FAQs
What happens if there is too little refrigerant?
Too little refrigerant will cause the system to underperform and struggle to remove heat effectively. The compressor may also overheat due to lack of proper refrigerant flow.
Can refrigerant be refilled without professional help?
No, refrigerant handling requires specialized training, tools, and an EPA license. Attempting to refill refrigerant without proper expertise can be dangerous.
Do all air conditioners use the same type of refrigerant?
No, different air conditioning systems may use different types of refrigerants based on their design and environmental regulations.
How often should refrigerant levels be checked?
Refrigerant levels should be checked annually by a professional HVAC technician as part of routine maintenance.
What are the signs of refrigerant leakage?
Signs of refrigerant leakage include hissing noises, ice buildup on refrigerant lines, and the air conditioner's inability to cool properly.
Can refrigerant be harmful to humans?
Yes, refrigerants can be toxic if inhaled or exposed to the skin or eyes. Proper safety precautions must be taken when handling refrigerants.
What causes refrigerant leaks?
Refrigerant leaks can be caused by loose connections, damaged refrigerant lines, corrosion, or wear and tear over time.
How is the correct refrigerant charge determined?
The correct refrigerant charge is determined by monitoring the system's temperature and pressure readings against the manufacturer's specifications.
Can an overcharged system be repaired?
In some cases, an overcharged system can be repaired by properly evacuating the excess refrigerant. However, severe overcharging may require component replacements.
What are the consequences of operating with contaminated refrigerant?
Contaminated refrigerant can cause increased wear and tear, reduced efficiency, and potential system failure if not addressed promptly.
Bình luận (0)
Bài viết đề xuất
Ensuring your vehicle's braking system is in top condition is crucial for safety on the road. One key component that requires periodic replacement is the brake rotors. The cost of replacing brake rotors can vary significantly based on several factors. This comprehensive guide will help you understand what influences these costs and how to make informed decisions to get the best value without compromising quality.
In the ever-evolving landscape of automotive engineering, fuel efficiency has become a paramount concern for both manufacturers and consumers alike. As the world grapples with the challenges of climate change and dwindling natural resources, the pursuit of vehicles that consume less fuel while delivering optimal performance has taken center stage.
The spark plug gap is a critical factor in the performance and efficiency of your Chevy 350 engine. A properly set gap ensures reliable ignition, optimal combustion, and maximum power output. In this comprehensive guide, we'll explore the importance of spark plug gap, its impact on engine operation, and the recommended specifications for Chevy 350 engines with both points and HEI ignition systems. Additionally, we'll walk you through the process of measuring and adjusting the gap, selecting the right spark plugs, and maintaining optimal performance over time.
Bài viết liên quan
Maintaining your vehicle's air conditioning system is crucial for ensuring a comfortable driving experience, especially during hot summer months. However, one of the most common issues that can compromise your car's AC performance is low refrigerant levels due to leaks
Maintaining the optimal refrigerant charge level is crucial for ensuring your vehicle's air conditioning system operates efficiently and effectively
Refrigerants are essential components in the operation of air conditioning, refrigeration, and heat pump systems. However, when these refrigerants become contaminated, they can pose severe risks to the environment, equipment, and even human health.