The diagnostic trouble code (DTC) P03E0 indicates that the engine control module (ECM) has detected low pressure in cylinder 8 of the engine. This code is part of the OBD-II system and is a generic code, meaning it has the same definition for all vehicles equipped with OBD-II self-diagnostic capabilities.
Alternator Environmental Performance: Efficiency in Extreme Conditions
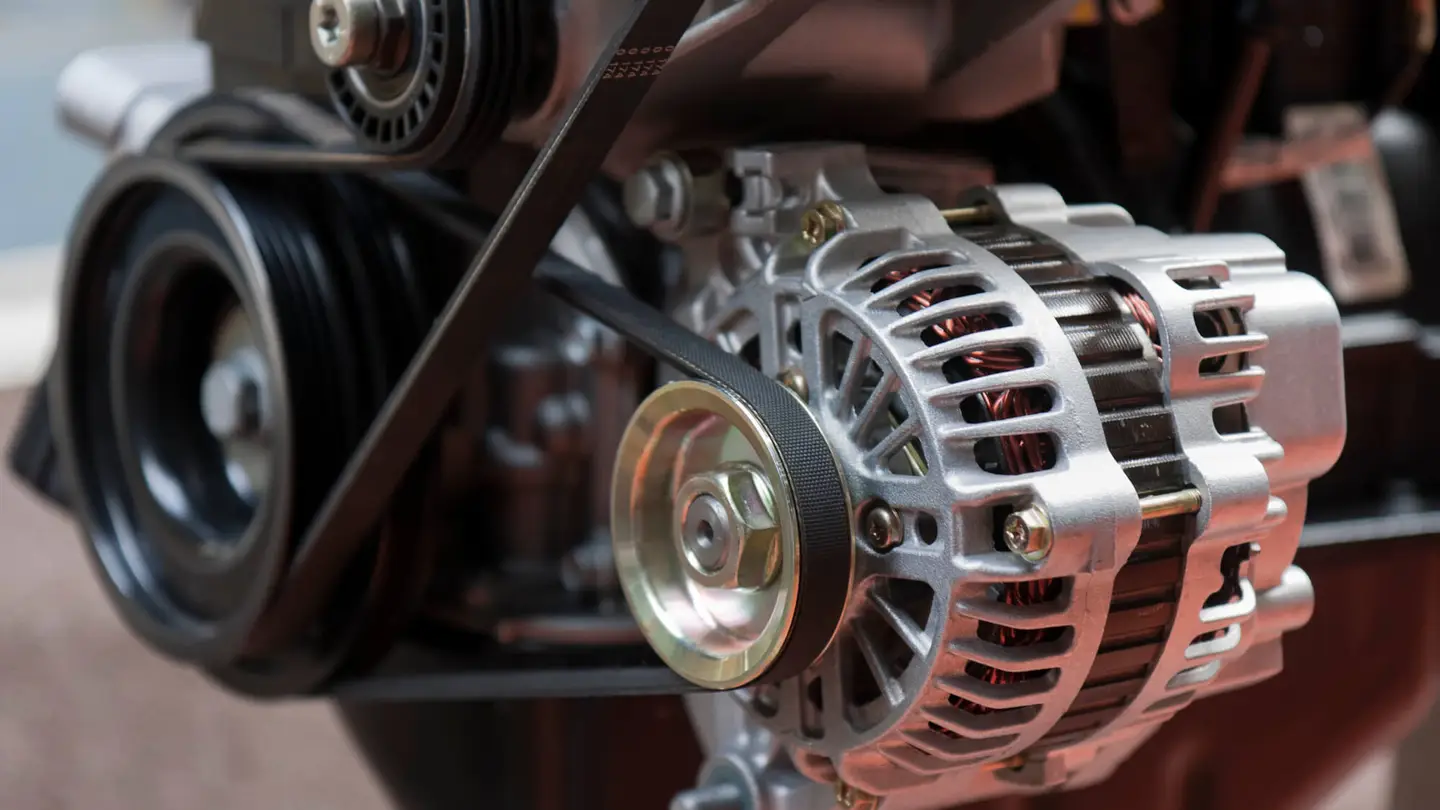
Alternator Environmental Performance: Efficiency in Extreme Conditions
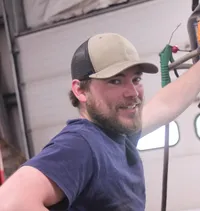
Alternators, the unsung heroes of a vehicle's electrical system, convert mechanical energy from the engine into electrical power to keep everything running smoothly. However, environmental factors like temperature and altitude can significantly impact their performance. In this article, we'll explore how alternators maintain efficiency in extreme conditions and discuss the latest advancements in alternator technology.
Introduction
Alternators are designed to operate reliably in a wide range of conditions, but their efficiency and output can be greatly affected by high temperatures and altitude. Understanding these impacts and the cutting-edge improvements in alternator design is crucial for ensuring optimal performance and reliability in any environment.
This comprehensive guide will cover:
Effects of temperature and altitude on alternator performance
Efficiency improvements in alternator design
Role of high-efficiency alternators in vehicle electrification
Best practices for proper alternator application and maintenance
Impact of Temperature on Alternators
Alternators operate most efficiently within a specific temperature range, typically between 25-40°C (77-104°F). When ambient temperatures rise above this optimal range, alternator performance can suffer in several ways:
Effect | Cause | Consequence |
---|---|---|
Reduced efficiency | Increased electrical resistance in windings | More energy lost as heat |
Overheating risk | Difficulty in heat dissipation | Premature failure |
Derated power output | Mitigation strategy | 3% reduction per 5°C above optimal range |
To combat the effects of high temperatures, proper cooling system design is essential. This includes:
Ensuring adequate airflow around the alternator
Using heat-resistant materials
Incorporating advanced cooling techniques like liquid cooling for extreme environments
By carefully managing heat buildup and optimizing cooling performance, modern alternators can maintain high efficiency and reliability even in hot, demanding conditions.
Altitude Effects on Alternator Performance
As elevation increases, air density decreases, reducing the effectiveness of air cooling systems. This thinner air makes it harder for the alternator to dissipate heat, causing it to run hotter than it would at lower altitudes.
Alternators are typically derated by around 3% for every 500 meters (1,640 feet) above 1,000 meters (3,280 feet) to prevent overheating and ensure reliable operation at high altitudes. However, the thinner air also reduces the dielectric strength of the air surrounding the components, presenting challenges for medium and high voltage alternators.
To maintain proper insulation and prevent electrical breakdown, these alternators may require:
Specialized winding insulation
Isolation transformers
By understanding the effects of altitude on alternator performance and designing systems to accommodate these challenges, manufacturers can ensure their products deliver reliable, efficient power generation in even the most demanding high-altitude environments.
Efficiency Improvements in Alternator Design
To meet the growing demands for high-efficiency, environmentally-friendly power generation, alternator manufacturers are continuously developing new technologies and design improvements:
Design Improvement | Benefit |
---|---|
Optimized electromagnetic designs | Minimize losses |
High-efficiency rectifier diodes | Lower power dissipation, faster switching |
Advanced cooling systems | Maximize heat dissipation, minimize parasitic losses |
Lightweight, compact designs | Reduce parasitic losses, increase power density |
Precise voltage regulation | Ensure optimal output, protect electrical components |
These advancements enable modern alternators to achieve efficiencies exceeding 80%, significantly reducing fuel consumption and emissions while delivering reliable, high-performance power generation.
Role of Efficient Alternators in Vehicle Electrification
As the automotive industry shifts towards electrification, high-efficiency alternators play a crucial role in improving overall vehicle efficiency. By maximizing alternator efficiency, less energy is wasted as heat, reducing engine load and improving fuel economy. This not only lowers operating costs for vehicle owners but also contributes to reduced emissions and a cleaner environment.
Efficient alternators enable advanced technologies like:
Smart charging systems that optimize alternator output based on electrical demands
Regenerative braking that converts kinetic energy from braking into electrical energy
The growing trend towards higher voltage electrical systems, such as 48V and above, allows for more efficient power transmission and enables the use of smaller, lighter components. High-efficiency alternators designed for these higher voltage systems will be essential for maximizing the benefits of electrification and helping to reduce transportation-related emissions.
Proper Alternator Application and Maintenance
To ensure that alternators deliver their full performance potential while operating within environmental limits, proper application and maintenance are essential.
Factors to consider when selecting an alternator:
Rated output
Efficiency
Temperature and altitude ratings
Compatibility with the vehicle's electrical system
Ensuring adequate airflow and cooling is critical for maintaining optimal performance and reliability. Regular maintenance tasks include:
Task | Frequency |
---|---|
Belt tension inspection and adjustment | Every 10,000 miles or 6 months |
Electrical connection inspection and cleaning | Every 20,000 miles or 12 months |
Bearing condition monitoring | Every 50,000 miles or 24 months |
Output and voltage regulation testing | Every 30,000 miles or 18 months |
Worn or damaged component replacement | As needed |
In extreme operating conditions, such as high temperatures or altitudes, derating alternator performance may be necessary to prevent overheating and ensure reliable operation. This can be achieved through proper application engineering, taking into account the specific environmental factors and adjusting alternator output accordingly.
Conclusion
Alternator efficiency and performance are greatly influenced by environmental factors, particularly temperature and altitude. As the demand for high-efficiency, eco-friendly power generation grows, manufacturers are responding with innovative designs and technologies that push the boundaries of alternator performance.
The role of high-efficiency alternators in reducing emissions and improving overall vehicle efficiency is becoming increasingly important as vehicle electrification gains momentum. By enabling technologies like smart charging and regenerative braking, and supporting the trend towards higher voltage electrical systems, efficient alternators are paving the way for a more sustainable future in transportation.
However, to fully realize the benefits of these advanced alternators, proper application and maintenance are crucial. By selecting the right alternator for the job, ensuring adequate cooling and airflow, and following recommended maintenance practices, vehicle owners and operators can maximize alternator performance and longevity, even in challenging environmental conditions.
As the automotive industry continues to evolve and adapt to the demands of a changing world, the importance of alternator efficiency and performance will only continue to grow. By staying at the forefront of alternator technology and best practices, we can work towards a cleaner, more sustainable future for transportation, one alternator at a time.
FAQs
What is the optimal temperature range for alternator operation?
Alternators are designed to operate most efficiently within a temperature range of 25-40°C (77-104°F). Operating outside this range can lead to reduced performance and potential damage.
How does high altitude affect alternator performance?
At high altitudes, the thinner air reduces the effectiveness of air cooling systems, causing alternators to run hotter. This can lead to reduced power output and potential overheating issues.
What is the typical derating factor for alternators at high altitudes?
Alternators are typically derated by around 3% for every 500 meters (1,640 feet) above 1,000 meters (3,280 feet) to prevent overheating and ensure reliable operation at high altitudes.
What are some of the latest advancements in alternator design for improved efficiency?
Recent advancements in alternator design include optimized electromagnetic designs, high-efficiency rectifier diodes, advanced cooling systems, lightweight and compact designs, and precise voltage regulation. These improvements help maximize efficiency and minimize losses.
How do high-efficiency alternators contribute to vehicle electrification efforts?
High-efficiency alternators play a crucial role in improving overall vehicle efficiency by reducing energy waste and enabling advanced technologies like smart charging systems and regenerative braking. This helps lower emissions and supports the trend towards electrification.
What factors should be considered when selecting an alternator for a specific application?
When selecting an alternator, important factors to consider include the rated output, efficiency, temperature and altitude ratings, and compatibility with the vehicle's electrical system. Proper application engineering is essential for optimal performance.
How often should alternator belts be inspected and adjusted?
Alternator belts should be inspected for proper tension and adjusted if necessary every 10,000 miles or 6 months to ensure optimal performance and prevent premature wear.
What is the recommended frequency for inspecting and cleaning alternator electrical connections?
Electrical connections should be inspected and cleaned every 20,000 miles or 12 months to maintain proper conductivity and prevent corrosion-related issues.
How can vehicle owners and operators maximize alternator performance and longevity?
To maximize alternator performance and longevity, vehicle owners and operators should select the right alternator for the job, ensure adequate cooling and airflow, and follow recommended maintenance practices, such as regular belt tension checks and electrical connection cleaning.
What role do high-efficiency alternators play in creating a more sustainable future for transportation?
High-efficiency alternators contribute to a more sustainable future for transportation by reducing emissions, improving overall vehicle efficiency, and enabling the adoption of advanced technologies like smart charging and regenerative braking. As the industry shifts towards electrification, the importance of efficient alternators will continue to grow.
Bình luận (0)
Bài viết đề xuất
In today's automotive world, choosing the right motor oil is crucial for ensuring optimal engine performance, protection, and longevity. While conventional mineral-based oils have been the industry standard for decades, synthetic motor oils have gained immense popularity due to their superior capabilities.
The exhaust manifold is a critical component that plays a pivotal role in optimizing an engine's performance. This comprehensive guide delves into the intricate details of exhaust manifolds, exploring their design, function, and impact on engine efficiency.
The diagnostic trouble code (DTC) P03AA indicates an issue with the cylinder pressure sensor circuit for cylinder 3. This code suggests that the engine control module (ECM) has detected an abnormal voltage or signal from the cylinder 3 pressure sensor, which is outside of the expected operating range or performance parameters.
Bài viết liên quan
Alternator recycling is a crucial process that helps conserve valuable resources, reduce waste, and minimize the environmental impact of the automotive industry. By recycling alternators, we can recover valuable metals and create a more sustainable future.