As an experienced automotive mechanic, I've encountered numerous cases where car owners face the frustrating issue of their vehicle refusing to start when the engine is hot. This problem can be perplexing and leave you stranded, especially during hot summer days
The Exhaust Manifold: Unlocking Engine Performance Potential
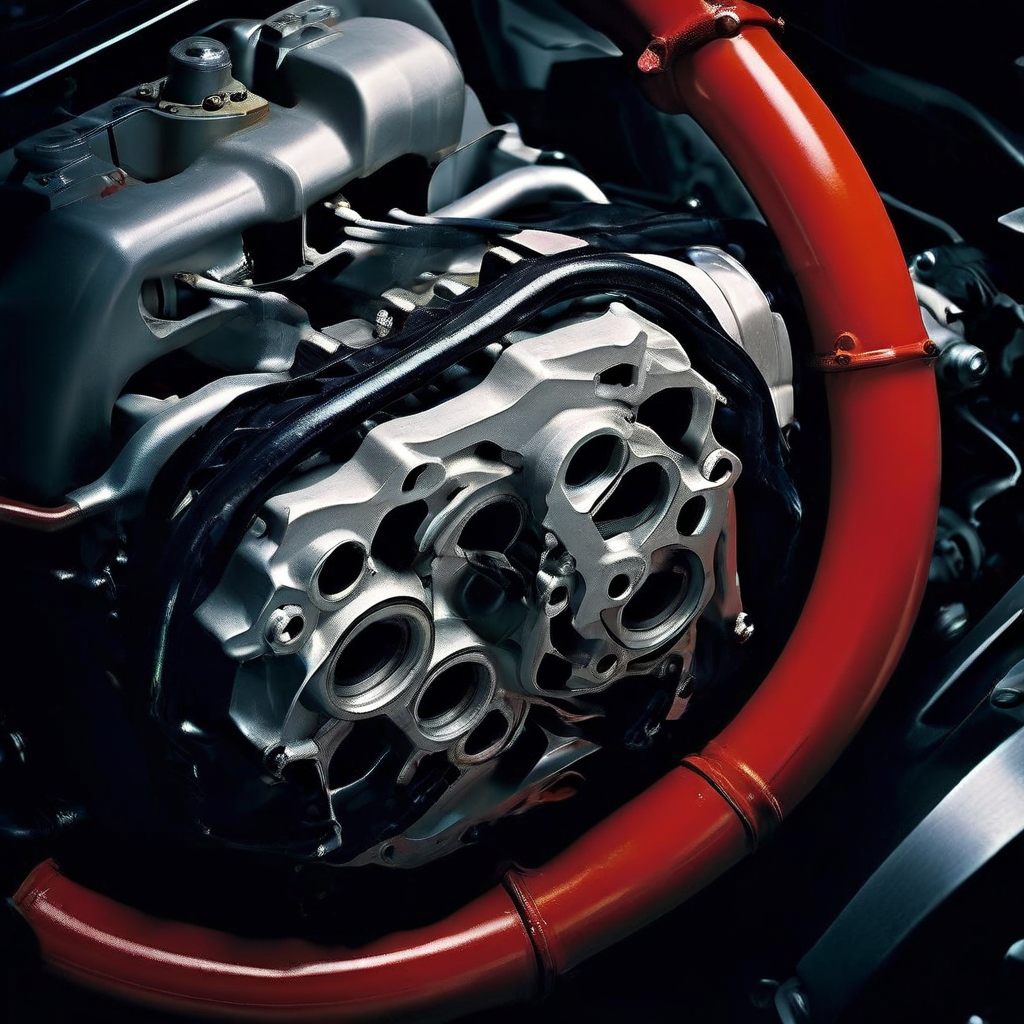
The Exhaust Manifold: Unlocking Engine Performance Potential
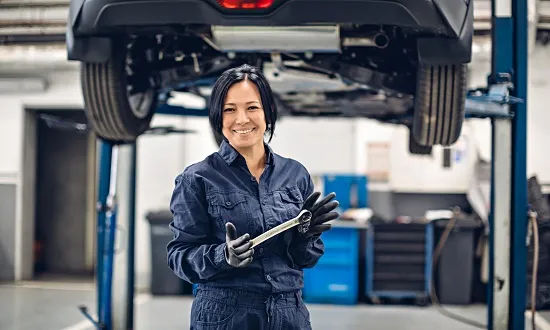
The exhaust manifold is a critical component that plays a pivotal role in optimizing an engine's performance. This comprehensive guide delves into the intricate details of exhaust manifolds, exploring their design, function, and impact on engine efficiency. By understanding the nuances of this essential component, vehicle owners and enthusiasts can make informed decisions to enhance their driving experience and maximize their engine's potential.
Introduction
An exhaust manifold is a series of interconnected pipes or runners attached to the engine's cylinder head. Its primary function is to collect the hot, pressurized exhaust gases expelled from multiple cylinders during the exhaust stroke and channel them into a single exhaust pipe. This amalgamation of individual exhaust streams facilitates efficient evacuation and subsequent treatment of the gases before their release into the atmosphere.
The exhaust manifold plays a crucial role in optimizing engine performance by reducing backpressure and enhancing the scavenging effect. Backpressure refers to the resistance faced by exhaust gases as they flow through the exhaust system, hindering the engine's ability to expel spent gases effectively. A well-designed manifold minimizes this resistance, allowing the engine to breathe more efficiently and produce more power. Moreover, the scavenging effect, facilitated by the manifold's design, helps remove residual exhaust gases from the cylinders, preparing them for the next intake stroke. By optimizing the length, diameter, and layout of the runners, manufacturers can enhance this effect, resulting in improved engine efficiency and overall performance.
Function and Working Principle
The exhaust manifold's primary function is to facilitate the efficient evacuation of exhaust gases from the engine cylinders. As the piston moves upward during the exhaust stroke, the exhaust valve opens, allowing the high-pressure, hot exhaust gases to escape into the manifold's runners. These gases are then channeled through the manifold and into the collector, where they merge into a single stream before entering the rest of the exhaust system.
Proper exhaust manifold design is crucial for reducing backpressure, a phenomenon that can significantly impact engine performance. Backpressure occurs when exhaust gases encounter resistance as they flow through the exhaust system, hindering the engine's ability to expel spent gases effectively. A well-designed manifold minimizes this resistance by optimizing the flow of exhaust gases, allowing the engine to breathe more efficiently and produce more power.
The scavenging effect is another critical aspect influenced by the exhaust manifold's design. As the exhaust gases exit the cylinder, they create a low-pressure wave that helps pull the remaining exhaust gases out of the cylinder, preparing it for the next intake stroke. By optimizing the length and diameter of the runners, as well as the layout of the manifold, manufacturers can enhance the scavenging effect, resulting in improved engine efficiency and performance.
The exhaust manifold's role in reducing backpressure and enhancing the scavenging effect directly impacts the engine's ability to breathe effectively. Efficient exhaust gas evacuation and cylinder preparation for the next intake stroke ensure that the engine can draw in fresh air and fuel mixture more easily, leading to improved combustion and increased power output.
Types of Exhaust Manifolds
Exhaust manifolds are available in various materials and designs, each offering unique advantages and suitability for different applications. Understanding the characteristics of these manifold types can help vehicle owners and enthusiasts make informed decisions based on their specific needs and performance goals.
Manifold Type | Material | Advantages | Applications |
---|---|---|---|
Cast Iron Manifolds | Cast Iron | Durability, Cost-Effectiveness | Standard, Non-Performance Engines |
Stainless Steel Manifolds | Stainless Steel | Corrosion Resistance, Performance | Performance Applications, Harsh Environments |
Tubular Headers | Stainless Steel | Improved Exhaust Flow, Reduced Interference | High-Performance Engines |
Ceramic-Coated Manifolds | Cast Iron or Stainless Steel with Ceramic Coating | Thermal Insulation, Heat Management | Performance and Efficiency Applications |
Cast Iron Manifolds
Cast iron exhaust manifolds are widely used in many vehicles due to their durability and cost-effectiveness. These manifolds are known for their ability to withstand extreme temperatures and harsh operating conditions, making them a reliable choice for standard, non-performance-oriented engines. While cast iron manifolds may not offer the same level of performance as more advanced designs, they are well-suited for standard engines where durability and affordability are prioritized over outright performance gains. Their rugged construction and relatively simple design make them a practical choice for everyday driving conditions.
Stainless Steel Manifolds
Stainless steel exhaust manifolds are renowned for their exceptional corrosion resistance, making them a popular choice for performance applications and harsh environments. Unlike cast iron, stainless steel is highly resistant to the corrosive effects of exhaust gases, ensuring long-lasting performance and durability. In addition to their corrosion-resistant properties, stainless steel manifolds are often designed with performance in mind. Their construction allows for more efficient exhaust flow and reduced backpressure, resulting in increased power output and improved throttle response. Many aftermarket performance exhaust manifolds and headers are made from stainless steel to cater to the demands of enthusiasts and high-performance vehicles.
Tubular Headers
Tubular headers, also known as extractor manifolds, feature individual pipes for each cylinder, which merge further downstream. This design helps reduce interference between cylinders and optimizes exhaust flow, resulting in increased power and throttle response. By separating the exhaust streams from each cylinder until they merge downstream, tubular headers minimize the interference and turbulence that can occur in traditional manifold designs. This reduction in interference allows for more efficient exhaust gas evacuation, contributing to improved engine performance.
Ceramic-Coated Manifolds
Some exhaust manifolds are coated with a ceramic material, which acts as an insulator, reducing heat transfer to the engine compartment and improving thermal efficiency. This insulation helps maintain higher exhaust gas temperatures, which can enhance performance and reduce emissions. In addition to improving thermal efficiency, ceramic-coated manifolds also play a role in heat management. By reducing the amount of heat radiated into the engine compartment, these manifolds help protect other engine components from excessive heat exposure, which can lead to premature wear and potential damage.
Design Considerations
The design of an exhaust manifold is influenced by several factors, including the engine configuration, the number of cylinders, and the desired performance characteristics. Manufacturers carefully consider various design elements to optimize exhaust flow, reduce backpressure, and enhance the scavenging effect, ultimately improving overall engine performance.
Design Factor | Considerations |
---|---|
Engine Configuration | Inline or V-type layout, positioning of cylinders |
Number of Cylinders | Determine the number of runners required |
Performance Goals | Maximum power output, throttle response, or efficiency |
Pipe Length and Diameter | Optimize for backpressure reduction and scavenging effect |
Manifold Layout | Minimize interference, reduce turbulence, optimize flow |
Noise Reduction | Incorporate bends, chambers, or resonators |
Heat Dissipation | Insulation and heat shielding techniques |
The engine configuration, such as inline or V-type, plays a significant role in the design of the exhaust manifold. The layout and positioning of the cylinders dictate the arrangement of the runners and the overall shape of the manifold, ensuring efficient exhaust gas collection and routing.
The number of cylinders in an engine directly impacts the number of runners required in the exhaust manifold. Manufacturers must carefully design the manifold to accommodate the specific cylinder count, ensuring proper exhaust gas flow and minimizing interference between individual streams.
When designing an exhaust manifold, manufacturers consider the desired performance goals for the engine. High-performance applications may require manifolds optimized for maximum power output and throttle response, while efficiency-focused designs prioritize reducing backpressure and enhancing the scavenging effect.
The length and diameter of the individual runners in the exhaust manifold are critical design considerations. Optimizing these dimensions can help reduce backpressure, enhance the scavenging effect, and improve overall exhaust gas flow, contributing to increased engine performance.
The layout of the manifold, including the positioning of the runners and the collector, plays a crucial role in exhaust gas evacuation. Manufacturers carefully design the manifold layout to minimize interference between individual exhaust streams, reduce turbulence, and optimize flow characteristics.
Exhaust manifold design also considers noise reduction strategies. By incorporating specific bends, chambers, or resonators, manufacturers can mitigate excessive exhaust noise, ensuring a more pleasant driving experience while complying with noise regulations.
Proper heat dissipation is another important consideration in exhaust manifold design. Manufacturers employ various techniques, such as insulation and heat shielding, to protect other engine components from excessive heat exposure, which can lead to premature wear and potential damage.
Installation and Maintenance
Proper installation and regular maintenance of the exhaust manifold are essential for ensuring optimal performance, longevity, and safety. Adhering to manufacturer guidelines and addressing any issues promptly can prevent further damage and ensure the continued efficient operation of the vehicle.
Proper Installation
Torque Specifications: Correct installation of the exhaust manifold is crucial to prevent exhaust leaks and ensure proper sealing. Manufacturers provide specific torque specifications for bolting the manifold to the cylinder head, and following these guidelines is essential for a secure and leak-free installation.
Gasket Selection: Using the correct gaskets is equally important during installation. Gaskets act as seals between the manifold and the cylinder head, preventing exhaust gas leaks and ensuring efficient exhaust flow. Selecting the appropriate gasket material and following the manufacturer's recommendations is vital for a successful installation.
Regular Inspections
Leak Detection: Over time, exhaust manifolds can develop leaks due to the extreme operating conditions they endure. Regular inspections are recommended to identify any potential leaks, which can be indicated by unusual noises, smells, or decreased engine performance. Addressing leaks promptly can prevent further damage and maintain optimal engine efficiency.
Crack Identification: In addition to leaks, exhaust manifolds can also develop cracks due to thermal stress and fatigue. Regular visual inspections can help identify any cracks or damage, allowing for timely replacement or repair before more significant issues arise.
Maintenance Importance
Regular maintenance of the exhaust manifold is crucial for ensuring its longevity and preventing potential performance issues or safety hazards. Neglecting maintenance can lead to blockages, excessive backpressure, and even exhaust leaks, all of which can negatively impact engine performance and potentially compromise the vehicle's emissions compliance.
Performance and Aftermarket Options
For those seeking increased power, improved throttle response, and an enhanced exhaust note, aftermarket performance exhaust manifolds or headers are popular upgrades. These components are designed to optimize exhaust flow, reduce backpressure, and improve the scavenging effect, resulting in gains in horsepower and torque.
Horsepower and Torque Gains
One of the primary benefits of aftermarket performance exhaust manifolds is the potential for horsepower and torque gains. By reducing backpressure and optimizing exhaust flow, these upgrades can unlock additional power from the engine, resulting in improved acceleration and overall performance.
Throttle Response Improvement
In addition to power gains, aftermarket manifolds can also enhance throttle response. By facilitating more efficient exhaust gas evacuation, these upgrades can improve the engine's responsiveness to throttle inputs, providing a more engaging and dynamic driving experience.
Exhaust Note Enhancement
Many enthusiasts seek aftermarket exhaust manifolds or headers not only for performance gains but also for the distinctive exhaust note they can produce. These components can alter the sound characteristics of the exhaust, creating a more aggressive and sporty tone that appeals to driving enthusiasts.
Compatibility Considerations
When considering aftermarket exhaust manifold options, it is essential to ensure compatibility with your specific vehicle. Factors such as engine configuration, cylinder count, and performance goals must be taken into account to ensure proper fitment and optimal performance gains.
Emissions Compliance
In some regions, aftermarket exhaust modifications may be subject to emissions regulations and compliance requirements. It is crucial to research and understand the applicable laws and regulations in your area to ensure that any performance upgrades do not compromise emissions compliance or result in legal issues.
Conclusion
The exhaust manifold is a critical component that plays a pivotal role in optimizing engine performance. By facilitating efficient exhaust gas evacuation, reducing backpressure, and enhancing the scavenging effect, a well-designed manifold can unlock the full potential of an engine. Understanding the various types, design considerations, and maintenance requirements of exhaust manifolds empowers vehicle owners and enthusiasts to make informed decisions that enhance their driving experience and maximize their engine's capabilities.
FAQs
What is the purpose of an exhaust manifold?
An exhaust manifold collects exhaust gases from the engine cylinders and channels them into the exhaust system. It plays a crucial role in optimizing engine performance by reducing backpressure and enhancing the scavenging effect.
What are the common materials used for exhaust manifolds?
The most common materials used for exhaust manifolds are cast iron and stainless steel, with cast iron being more cost-effective and stainless steel offering better corrosion resistance.
What is the difference between a four-into-one and a four-into-two exhaust manifold design?
A four-into-one design combines all four runners into a single collector, while a four-into-two design first pairs the runners into two before merging them into a single collector.
How does the exhaust manifold design affect engine performance?
The design of the exhaust manifold, including the length, diameter, and layout of the runners, can significantly impact backpressure, scavenging effect, and overall exhaust gas flow, directly influencing engine performance.
What is the purpose of ceramic coating on exhaust manifolds?
Ceramic coating on exhaust manifolds acts as an insulator, reducing heat transfer to the engine compartment and improving thermal efficiency, while also aiding in heat management.
Why is proper installation and maintenance of the exhaust manifold important?
Proper installation and regular maintenance of the exhaust manifold are crucial to prevent exhaust leaks, ensure efficient exhaust flow, and maintain optimal engine performance and safety.
What are the advantages of aftermarket performance exhaust manifolds?
Aftermarket performance exhaust manifolds can offer benefits such as increased horsepower and torque, improved throttle response, and an enhanced exhaust note due to optimized exhaust flow and reduced backpressure.
How do exhaust manifolds contribute to emission control?
Exhaust manifolds play a role in emission control by efficiently directing exhaust gases from the engine cylinders to the exhaust system, where they can be treated and filtered before release into the atmosphere.
What is the significance of tuned-length exhaust manifolds?
Tuned-length exhaust manifolds are designed to create resonance in the exhaust system, enhancing the scavenging effect and improving engine performance, particularly at higher RPM ranges.
How do exhaust manifolds affect engine durability?
Exhaust manifolds are subjected to extreme temperatures and thermal stress, which can lead to fatigue and potential failure over time. Proper design and material selection are crucial for ensuring the manifold's longevity and preventing premature wear or damage to other engine components.
Bình luận (0)
Bài viết đề xuất
The impact of car exhaust emissions on acid rain formation is a pressing environmental concern with far-reaching consequences. This article delves into the alarming effects of vehicular pollution on the acidification of precipitation and explores effective strategies to mitigate this global issue.
The air filter is a critical component in a vehicle's engine, responsible for trapping contaminants such as dust, dirt, and debris before they enter the combustion chamber. However, sometimes oil can find its way into the air filter housing or onto the filter itself, which is not a normal occurrence and can indicate underlying issues that need to be addressed.
Your hazard lights are a crucial safety feature, alerting other drivers to potential dangers or emergencies on the road. However, when they refuse to turn off, it can be frustrating and potentially hazardous. This guide will help you understand the common causes and provide practical solutions to resolve the issue efficiently.
Bài viết liên quan
The internal combustion engine is a remarkable invention that has revolutionized transportation and industry.
A crankshaft is a critical component found in internal combustion engines, which are widely used in various applications, including automobiles, trucks, generators, and industrial machinery
Camshafts are a critical component in internal combustion engines, responsible for precisely controlling the opening and closing of the engine's intake and exhaust valves. This intricate coordination of valve movement is fundamental for an engine's performance, efficiency, and power output.
In the ever-evolving automotive industry, valves play a pivotal role in regulating and controlling the flow of various fluids, gases, and air-fuel mixtures. From engine components to braking systems, these mechanical marvels ensure efficient and reliable performance.
Spark plugs are essential components that play a crucial role in the operation of gasoline-powered internal combustion engines. They are responsible for igniting the air-fuel mixture within the engine's combustion chamber, initiating the combustion process that powers the vehicle
A timing belt, also known as a cambelt, is a critical component in an internal combustion engine that synchronizes the rotation of the crankshaft and camshaft(s).
The cylinder head is an intricate and indispensable component that sits atop the engine block, orchestrating the intricate dance of combustion that propels your vehicle forward.
An intake manifold plays a pivotal role in an internal combustion engine's performance by evenly distributing the air/fuel mixture to each cylinder. This comprehensive guide delves into the intricacies of this critical component, exploring its design, types, materials, performance modifications, installation, and maintenance aspects.