The P0015 diagnostic trouble code signals an issue with the camshaft timing system on the engine's bank 1 (the cylinder bank housing cylinder #1). Specifically, it indicates that the exhaust camshaft timing is over-retarded or retarded beyond the engine control module's (ECM/PCM) commanded position. Neglecting this condition can lead to drivability problems and potential engine damage. This article aims to shed light on the underlying causes, symptoms, diagnostic procedures, and repair methods for the P0015 code.
What is an Intake Manifold? The Essential Guide for Car Enthusiasts
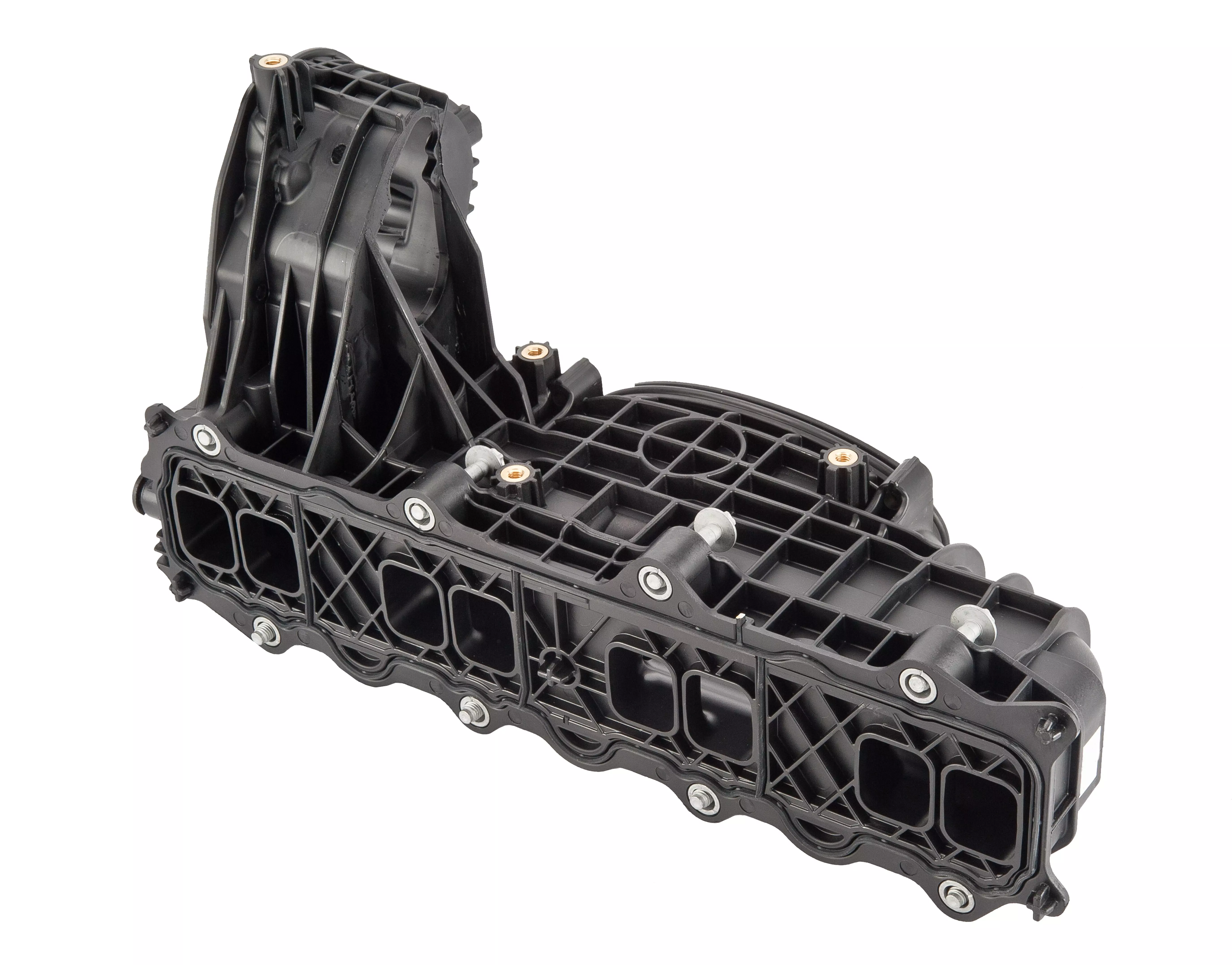
What is an Intake Manifold? The Essential Guide for Car Enthusiasts
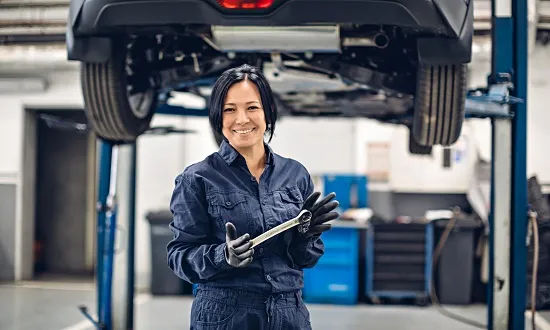
An intake manifold plays a pivotal role in an internal combustion engine's performance by evenly distributing the air/fuel mixture to each cylinder. This comprehensive guide delves into the intricacies of this critical component, exploring its design, types, materials, performance modifications, installation, and maintenance aspects.
Introduction to Intake Manifolds
The intake manifold, also known as the inlet manifold, is an integral part of an engine's induction system. Its primary function is to distribute the combustible air/fuel mixture from the throttle body or carburetor to the individual cylinders. By ensuring an even distribution, the intake manifold optimizes the engine's combustion process, leading to improved power output and efficiency.
Key Points | |
---|---|
Definition | A series of interconnected passages that channel the air/fuel mixture from a single source to multiple destinations (cylinders). |
Purpose | Minimize turbulence and resistance, ensuring smooth and consistent airflow to each cylinder. |
Importance | Influences the volumetric efficiency of the combustion process, impacting power output, fuel economy, and emissions. |
Types of Intake Manifolds
Intake manifolds come in various designs, each tailored to specific engine configurations and performance requirements. Understanding the different types is essential for selecting the appropriate manifold for your vehicle.
Type | Description | Characteristics | Applications |
---|---|---|---|
Dual-Plane | Two separate plenums feeding cylinders | Longer runners, cleaner induction pulse at low RPM | Street performance, mild racing |
Single-Plane | Single open plenum feeding all cylinders | Excels at high RPM power delivery | High-performance, racing |
Tuned/Ram | Utilizes induction pulses and resonance effects | Long runners, divided plenum | Specific RPM range optimization |
Air-Gap | Incorporates air gap between plenum and runners | Reduces heat buildup | Thermal management |
Design and Components
The design and components of an intake manifold play a crucial role in its performance and efficiency. Understanding these elements is essential for optimizing the engine's power output.
Plenum: The large cavity acting as a reservoir, holding the air/fuel mixture until distribution. Its size and shape significantly impact performance characteristics.
Runners: Tubes carrying the air/fuel mixture from the plenum to the intake ports on each cylinder head. Their length, diameter, and taper determine peak horsepower and torque.
Ports: In fuel-injected engines, each runner has ports for fuel injectors, introducing fuel into the air stream before entering the intake port. Their design and positioning influence mixture preparation and combustion efficiency.
Materials and Construction
Material | Advantages | Disadvantages |
---|---|---|
Cast Iron | Durable, withstands high temperatures | Relatively heavy |
Cast Aluminum | Lighter, better heat dissipation | - |
Plastic | Cost-effective, lightweight | May not handle high temperatures well, susceptible to warpage/cracking |
The manufacturing process typically involves casting (for metal manifolds) or molding (for plastic manifolds).
Performance Modifications
To enhance airflow and increase power output, various performance modifications can be made to intake manifolds. These modifications can unlock the engine's full potential and cater to specific performance goals.
Porting and Polishing: Smoothing and reshaping the intake ports and runners to improve airflow, done by hand or using CNC machining. Suitable for high-RPM applications.
Adding Spacers or Air Gaps: Installing spacers or incorporating air gaps between the plenum and runners to reduce heat buildup and improve performance, beneficial for engines operating at high temperatures or in demanding conditions.
Aftermarket Performance Manifolds: Many aftermarket companies offer performance intake manifolds designed with larger plenums, optimized runner designs, and other enhancements tailored to specific engines and applications, providing substantial power gains and improved airflow characteristics.
Installation and Maintenance
Proper installation and regular maintenance are essential for ensuring the longevity and optimal performance of an intake manifold.
Installation Considerations:
Use correct gaskets
Follow manufacturer's torque specifications
Improper installation can lead to vacuum leaks, impacting engine performance and efficiency
Common Issues and Maintenance:
Cracks
Vacuum leaks
Carbon buildup
Regular cleaning and inspection for leaks can prevent these problems and ensure proper engine operation
Conclusion
The intake manifold is a critical component in an internal combustion engine, playing a vital role in distributing the air/fuel mixture evenly to each cylinder. By understanding the different types, designs, materials, and performance modifications available, car enthusiasts can make informed decisions to optimize their engine's performance and ensure its longevity. Proper installation and regular maintenance are essential for maximizing the benefits of an optimized intake manifold system.
This comprehensive guide has covered the key aspects of intake manifolds, including their definition, purpose, types, design components, materials, performance modifications, installation considerations, and maintenance requirements. With this knowledge, you can better understand the importance of this crucial engine component and make informed decisions to enhance your vehicle's performance and efficiency.
FAQs
What is the difference between a dual-plane and single-plane intake manifold?
A dual-plane manifold has two separate plenums feeding the cylinders, while a single-plane manifold has one open plenum feeding all cylinders. Dual-plane designs excel at low RPM performance, while single-plane manifolds are better for high RPM power delivery.
What is the purpose of the plenum in an intake manifold?
The plenum is a large cavity that acts as a reservoir, holding the air/fuel mixture until it is distributed to the cylinders. Its size and shape significantly impact the engine's performance characteristics.
What are the advantages of porting and polishing an intake manifold?
Porting and polishing smooths and reshapes the intake ports and runners to improve airflow, which can unlock additional power, especially at high RPM. It is a common performance modification for high-performance engines.
Why are air gaps or spacers sometimes added to intake manifolds?
Air gaps or spacers are added between the plenum and runners to reduce heat buildup, which can improve performance, especially in engines operating at high temperatures or in demanding conditions.
What are the common materials used for intake manifolds?
The most common materials for intake manifolds are cast iron, cast aluminum, and plastic. Each material has its own advantages and disadvantages in terms of weight, heat dissipation, and cost.
What are the potential issues that can occur with intake manifolds?
Common issues with intake manifolds include cracks, vacuum leaks, and carbon buildup. Regular maintenance and inspection for leaks are essential to prevent these problems and ensure proper engine operation.
How can improper installation of an intake manifold affect engine performance?
Improper installation of an intake manifold can lead to vacuum leaks, which can significantly impact engine performance and efficiency. Following the manufacturer's torque specifications and using the correct gaskets is crucial.
What is the purpose of fuel injector ports in the intake manifold runners?
In fuel-injected engines, each runner has ports for fuel injectors, which introduce fuel into the air stream before entering the intake port. Their design and positioning influence mixture preparation and combustion efficiency.
Why are tuned or ram intake manifolds used?
Tuned or ram intake manifolds are designed to utilize induction pulses and resonance effects to optimize performance within a specific RPM range. They typically feature long runners and a divided plenum.
What is the importance of regular maintenance for intake manifolds?
Regular maintenance, such as cleaning and inspecting for leaks, is essential for ensuring the longevity and optimal performance of an intake manifold. Neglecting maintenance can lead to issues like carbon buildup and vacuum leaks, which can negatively impact engine performance.
Bình luận (0)
Bài viết đề xuất
When it comes to maintaining your vehicle's suspension system, choosing the right replacement parts is crucial for ensuring a smooth and safe ride. Mevotech, a Canadian company with over four decades of experience in the automotive aftermarket, has emerged as a trusted choice among professional technicians and DIY enthusiasts alike.
The exhaust system is a critical component of any internal combustion engine vehicle, responsible for expelling harmful gases, reducing emissions, and enhancing overall performance.
P03C3 is an OBD-II trouble code that indicates the engine control module (ECM) has detected abnormally high cylinder pressure in cylinder #5 of the engine. This code can be triggered by several potential issues related to the combustion process or mechanical problems in that specific cylinder.
Bài viết liên quan
The internal combustion engine is a remarkable invention that has revolutionized transportation and industry.
A crankshaft is a critical component found in internal combustion engines, which are widely used in various applications, including automobiles, trucks, generators, and industrial machinery
Camshafts are a critical component in internal combustion engines, responsible for precisely controlling the opening and closing of the engine's intake and exhaust valves. This intricate coordination of valve movement is fundamental for an engine's performance, efficiency, and power output.
In the ever-evolving automotive industry, valves play a pivotal role in regulating and controlling the flow of various fluids, gases, and air-fuel mixtures. From engine components to braking systems, these mechanical marvels ensure efficient and reliable performance.
Spark plugs are essential components that play a crucial role in the operation of gasoline-powered internal combustion engines. They are responsible for igniting the air-fuel mixture within the engine's combustion chamber, initiating the combustion process that powers the vehicle
A timing belt, also known as a cambelt, is a critical component in an internal combustion engine that synchronizes the rotation of the crankshaft and camshaft(s).
The cylinder head is an intricate and indispensable component that sits atop the engine block, orchestrating the intricate dance of combustion that propels your vehicle forward.
An intake manifold plays a pivotal role in an internal combustion engine's performance by evenly distributing the air/fuel mixture to each cylinder. This comprehensive guide delves into the intricacies of this critical component, exploring its design, types, materials, performance modifications, installation, and maintenance aspects.
The exhaust manifold is a critical component that plays a pivotal role in optimizing an engine's performance. This comprehensive guide delves into the intricate details of exhaust manifolds, exploring their design, function, and impact on engine efficiency.