Magnaflow and Flowmaster are two leading manufacturers of performance exhaust systems and mufflers for automobiles. Both companies have been in the industry for decades and have built a reputation for producing high-quality products that enhance the sound and performance of vehicles.
P03C1 - Cylinder 5 Pressure Sensor Circuit Intermittent/Erratic
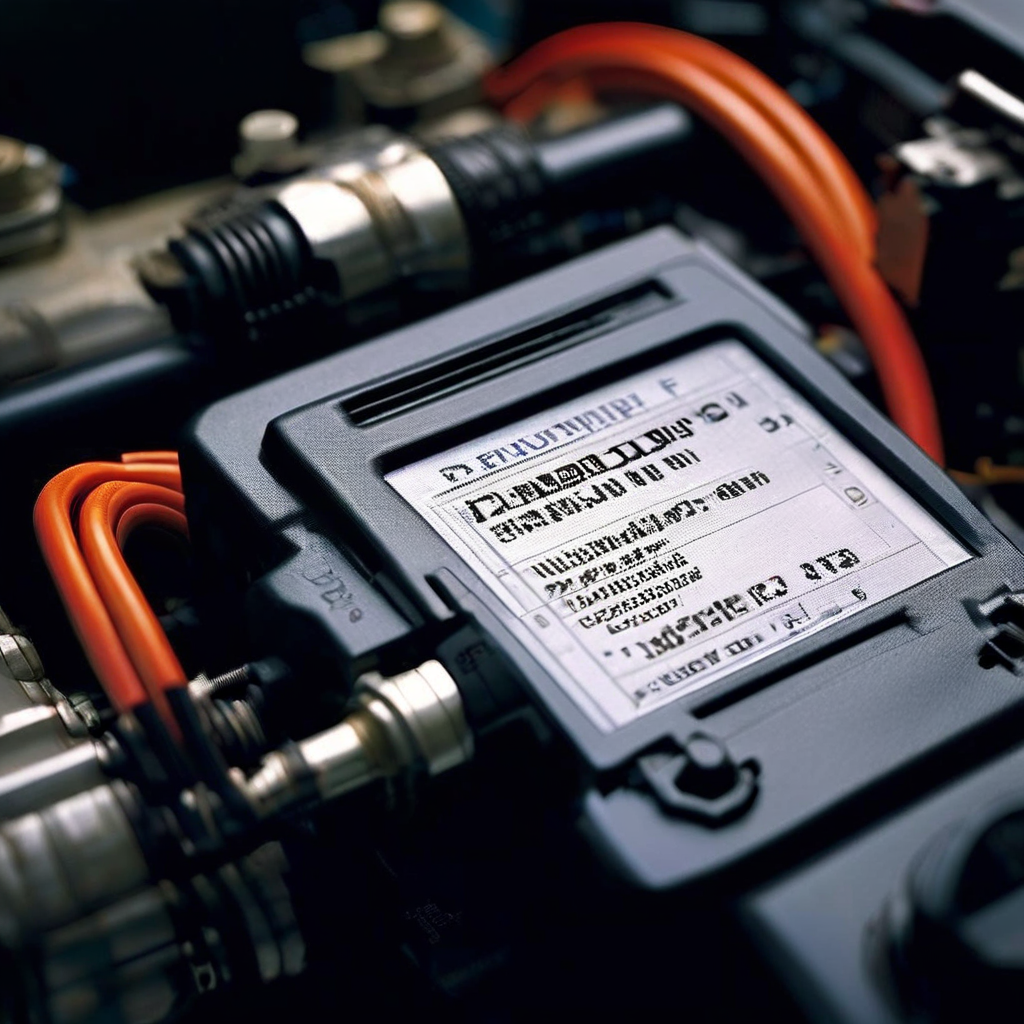
P03C1 - Cylinder 5 Pressure Sensor Circuit Intermittent/Erratic
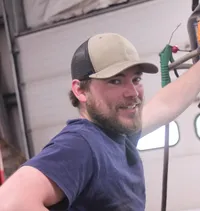
Introduction
The diagnostic trouble code (DTC) P03C1 indicates an issue with the cylinder 5 pressure sensor circuit in the engine. This sensor monitors the pressure inside cylinder 5 during the combustion process. The code is triggered when the powertrain control module (PCM) detects an intermittent or erratic signal from the pressure sensor circuit.
Understanding the Cylinder 5 Pressure Sensor
Before we delve into the troubleshooting process, let's first understand the role of the cylinder 5 pressure sensor. This sensor is a crucial component of the engine's electronic control system, responsible for monitoring the combustion pressure within cylinder 5.
Sensor Function | Description |
---|---|
Pressure Monitoring | The sensor measures the combustion pressure inside cylinder 5 during the engine's operation. |
Data Transmission | The sensor transmits the pressure data to the engine control module (ECM) for analysis and adjustments. |
Engine Optimization | The ECM uses the pressure data to optimize various engine parameters, such as fuel injection timing and ignition timing, ensuring optimal performance and emissions control. |
The data from this sensor is critical for the ECM to make real-time adjustments and maintain efficient engine operation.
Common Causes of the P03C1 Code
Over the years, I've encountered several common causes that can trigger the P03C1 code. Here are the main culprits:
Wiring Issues
Damaged, shorted, or corroded wiring between the cylinder 5 pressure sensor and the ECM can lead to intermittent or erratic readings. This can be caused by various factors, such as exposure to heat, moisture, or physical damage.
Damaged wiring insulation
Corroded or loose connectors
Shorts in the wiring harness
Faulty Cylinder 5 Pressure Sensor
The sensor itself may be defective or contaminated, causing it to send inaccurate or inconsistent readings to the ECM. This can happen due to normal wear and tear, exposure to extreme temperatures, or debris accumulation.
Sensor contamination
Internal sensor failure
Mechanical damage to the sensor
ECM Problems
In some cases, the issue may lie within the ECM itself. Software glitches, internal faults, or other ECM-related problems can lead to incorrect interpretations of the data from the pressure sensor.
Software glitches or bugs
Internal ECM faults or damage
Compatibility issues with sensor data
Diagnostic Steps: A Systematic Approach
When faced with the P03C1 code, I follow a systematic diagnostic approach to pinpoint the root cause efficiently. Here are the steps I typically take:
Visual Inspection
Inspect the wiring harness and connectors for signs of damage, corrosion, or loose connections.
Check for any physical obstructions or debris near the sensor or wiring.
Voltage and Ground Checks
Verify proper voltage supply to the pressure sensor.
Check for proper grounding of the sensor circuit.
Live Data Monitoring
Connect a scan tool and monitor the live data from the cylinder 5 pressure sensor.
Observe for erratic, implausible, or inconsistent readings.
Resistance Testing
Perform a resistance test on the pressure sensor to check if it is within specifications.
Out-of-range values typically indicate a failed sensor.
ECM Diagnostics
Check for any stored trouble codes related to the ECM or sensor circuit.
Perform ECM diagnostics to rule out internal faults or software issues.
Repair Instructions: Restoring Optimal Performance
Once the root cause has been identified, it's time to implement the appropriate repair. Here are the common repair procedures:
Wiring Repair or Replacement
Carefully repair or replace the damaged wiring or connectors in the cylinder 5 pressure sensor circuit.
Ensure proper connections, insulation, and routing of the wiring harness.
Sensor Replacement
If the cylinder 5 pressure sensor is found to be faulty or contaminated, replace it with a new, high-quality sensor that meets the manufacturer's specifications.
Follow the recommended installation procedures and torque specifications.
ECM Software Update or Replacement
In cases where the issue persists after checking the sensor and wiring, update the ECM software to address any software-related issues.
If the ECM is found to be faulty, replace it with a new or remanufactured unit.
Throughout the repair process, I strictly follow the manufacturer's service manual to ensure proper procedures and torque specifications are adhered to.
Preventing Future Occurrences
While repairs are necessary to resolve the immediate issue, I also emphasize preventive measures to minimize the likelihood of future problems. Here are some tips I recommend:
Regular Maintenance and Inspections
Perform regular maintenance and inspections on the engine's wiring harnesses and connectors.
Identify and address potential issues before they escalate.
Timely Sensor Replacement
Replace the cylinder pressure sensors at the recommended intervals or if they show signs of contamination or damage.
Proactive sensor replacement can prevent failures and associated issues.
Engine Bay Cleanliness
Keep the engine bay clean and free from debris that could potentially damage the wiring or sensors.
A clean environment can extend the lifespan of these components.
Proper Engine Operation and Driving Conditions
Follow the manufacturer's guidelines for proper engine operation and driving conditions.
Adhering to these recommendations can minimize stress on the engine components, including the pressure sensors.
Preventive Measure | Description |
---|---|
Regular Inspections | Inspect wiring, connectors, and sensors during routine maintenance. |
Timely Replacements | Replace sensors and components at recommended intervals. |
Engine Bay Cleanliness | Keep the engine bay free from debris and contaminants. |
Proper Operation | Follow manufacturer guidelines for engine operation and driving conditions. |
By implementing these preventive measures, you can significantly reduce the likelihood of encountering the P03C1 code or other related issues in the future.
Cost Considerations
When it comes to repairs related to the P03C1 code, the cost can vary depending on the root cause and the specific vehicle make and model. Here's a general breakdown of the potential costs:
Cylinder Pressure Sensor Replacement
Parts cost: $50 - $200 (depending on the sensor and vehicle model)
Labor cost: $50 - $150 (1-2 hours of labor)
Wiring Repair or Replacement
Parts cost: $50 - $300 (depending on the extent of the wiring damage)
Labor cost: $100 - $300 (2-4 hours of labor)
ECM Software Update or Replacement
Software update cost: $100 - $300 (depending on the vehicle and service provider)
ECM replacement cost: $500 - $1,500 (including parts and labor)
It's important to keep in mind that addressing these issues promptly can prevent further damage and more expensive repairs down the line. Regular maintenance and timely repairs can ultimately save you money in the long run.
Conclusion
Troubleshooting the P03C1 code – Cylinder 5 Pressure Sensor Circuit Intermittent/Erratic – requires a systematic approach and a deep understanding of the engine's electronic control system. By following the diagnostic steps, implementing the appropriate repairs, and adopting preventive measures, you can ensure your vehicle's optimal performance and longevity.
As an experienced mechanic, I've witnessed firsthand the importance of addressing these issues promptly and correctly. With the right knowledge, tools, and attention to detail, you can tackle this code and keep your vehicle running smoothly for years to come.
FAQs
What are the symptoms of a faulty cylinder 5 pressure sensor?
The most common symptoms include engine misfiring, poor fuel economy, and illuminated check engine light. The engine may also experience rough idling or lack of power.
How can I test the cylinder 5 pressure sensor without specialized tools?
You can perform a basic resistance test on the sensor using a multimeter. Consult the service manual for the correct resistance range.
Can a damaged wiring harness cause intermittent sensor readings?
Yes, a damaged or corroded wiring harness can lead to intermittent or erratic readings from the cylinder 5 pressure sensor.
Is it possible to clean and reuse a contaminated pressure sensor?
In most cases, it is recommended to replace a contaminated pressure sensor with a new one for optimal performance and reliability.
What are the consequences of ignoring the P03C1 code?
Ignoring this code can lead to further engine damage, increased emissions, and potential failure of other related components.
How often should cylinder pressure sensors be replaced?
Cylinder pressure sensors should be replaced at the recommended intervals specified by the manufacturer or when they show signs of failure.
Can improper engine operation contribute to pressure sensor issues?
Yes, operating the engine outside of the manufacturer's recommended conditions can accelerate wear and tear on components like pressure sensors.
Is it necessary to update the ECM software during repairs?
In some cases, updating the ECM software may be required to address any software-related issues or compatibility problems.
Can a faulty ECM cause inaccurate pressure sensor readings?
Yes, internal faults or software glitches within the ECM can lead to incorrect interpretations of the pressure sensor data.
What are the potential cost implications of ignoring pressure sensor issues?
Ignoring these issues can lead to more expensive repairs down the line, such as ECM replacement or engine damage.
Bình luận (0)
Bài viết đề xuất
Pre-mixed coolant is a ready-to-use automotive coolant designed to provide optimal protection for your vehicle's cooling system. It offers a convenient solution by providing a pre-formulated mixture of antifreeze and water, along with corrosion inhibitors and other additives. This comprehensive guide explores the composition, advantages, shelf life, disposal, and selection considerations of pre-mixed coolants, helping you make an informed decision for your vehicle's cooling needs.
If you're experiencing starting issues or electrical problems with your vehicle, a failing ignition switch could be the culprit. The ignition switch is a critical component that plays a vital role in your car's starting and electrical systems. In this comprehensive guide, we'll explore the common symptoms of a bad ignition switch, how to diagnose the problem, and what you can do to fix it.
As a driver, you rely on your vehicle's traction control system (TCS) to maintain optimal braking performance and stability, especially in challenging road conditions. The TCS prevents wheel lockup and skidding, ensuring a safer and more controlled driving experience. However, when a "Tbc Fault" or traction control system malfunction occurs, it can be concerning and potentially dangerous. In this article, we'll delve into the world of traction control systems, explore common causes of TCS faults, and provide strategies for diagnosing and resolving these issues to keep your vehicle's braking system in top shape.