The diagnostic trouble code (DTC) P03AD indicates an issue with the cylinder 3 pressure sensor circuit on the vehicle's engine. This sensor monitors the combustion pressure inside cylinder 3 and sends the data to the engine control module (ECM). The "intermittent/erratic" part of the code means the ECM is detecting an inconsistent or erratic signal from the sensor circuit.
Rust and Corrosion: Understanding the Difference for Effective Prevention
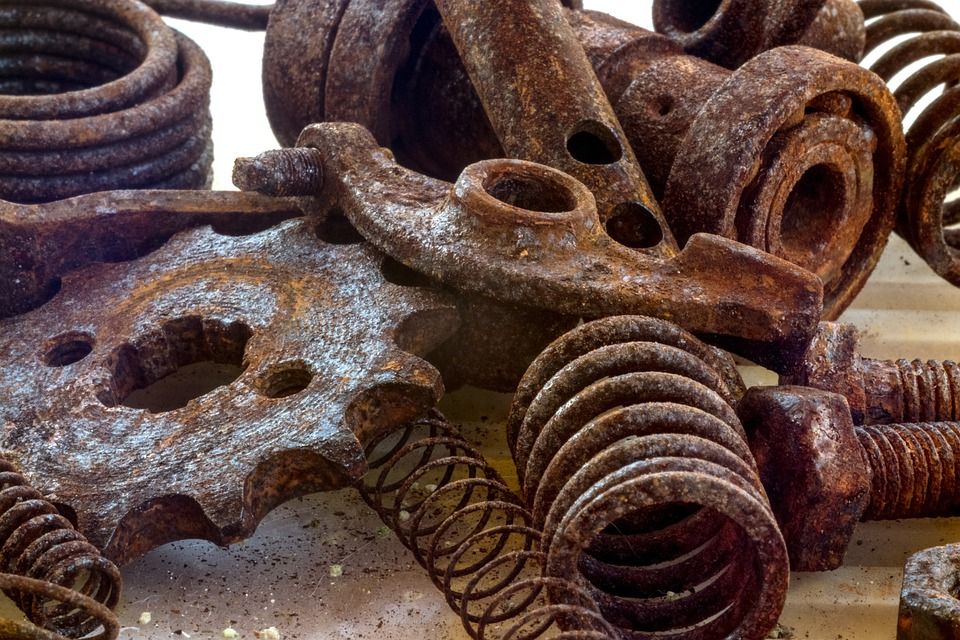
Rust and Corrosion: Understanding the Difference for Effective Prevention
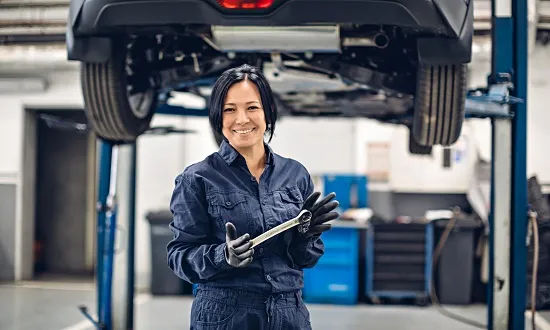
Introduction
Rust and corrosion are two terms that are often used interchangeably, but they are not the same. While rust is a specific form of corrosion, corrosion is a broader term that encompasses various types of material degradation. Understanding the difference between rust and corrosion is crucial for implementing effective prevention strategies and maintaining the integrity of materials, particularly metals.
The Culprits Behind Rust and Corrosion
Rust and corrosion are the result of a chemical reaction between metal and oxygen in the presence of moisture or other electrolytes. Let me break down the main culprits that contribute to this destructive process:
Cause | Description |
---|---|
Moisture | One of the most common causes is exposure to moisture in the air (humidity) or direct contact with water. When metal surfaces come into contact with water containing dissolved oxygen and minerals, an electrochemical reaction occurs, leading to the formation of iron oxides or rust. This is why vehicles in humid or coastal regions are particularly susceptible to corrosion. |
Salt Air | Exposure to saltwater or salt air, common in coastal regions, accelerates the rusting process. Saltwater contains high levels of chloride ions, which act as an electrolyte and facilitate the oxidation reaction. This is why vehicles near the ocean often show signs of corrosion much faster than those in inland areas. |
Acids and Chemicals | Acids and certain chemicals can also cause corrosion by reacting with the metal surface and promoting oxidation. In industrial settings where acids or chemicals like fertilizers and cleaning agents are used, vehicles and equipment are prone to this type of corrosion. |
Poor Maintenance | Lack of proper maintenance, such as not cleaning or coating metal surfaces, can lead to the accumulation of dirt and grime, providing a breeding ground for rust formation. Neglecting regular maintenance is a surefire way to invite corrosion onto your vehicle. |
Dissimilar Metals | When different metals are in contact, galvanic corrosion can occur due to the electrochemical potential difference between them, causing one metal to corrode faster than the other. This is why it's important to use compatible materials and avoid mixing dissimilar metals whenever possible. |
Stress Corrosion Cracking (SCC) | Metals under stress and exposed to corrosive environments, such as high temperatures or certain chemicals, can experience stress corrosion cracking, which affects materials like stainless steel and aluminum. This type of corrosion can be particularly dangerous as it can lead to sudden and catastrophic failures. |
Microbial Corrosion | Some microorganisms can produce acidic compounds that corrode metal surfaces, especially in the presence of moisture and nutrients. This type of corrosion is often seen in areas with stagnant water or organic matter buildup. |
Fretting Corrosion | This type of wear corrosion occurs on surfaces in contact with each other during movement or vibration, creating small particles that can form an electrolyte and lead to further damage. This is a common issue in suspension components and other moving parts of vehicles. |
Identifying the Signs of Rust and Corrosion
As a mechanic, one of the first steps in addressing rust and corrosion is to identify the problem areas. Here are some tips for inspecting and identifying these issues:
Visual Inspection: Look for signs of rust, such as reddish-brown flaky deposits, pitting, or discoloration on metal surfaces.
Check for Moisture: Use a moisture meter or inspect for sources of water leaks, condensation, or high humidity areas.
Test for Salinity: In coastal regions, test for the presence of salt deposits using a salt meter or conductivity meter.
Identify Dissimilar Metals: Check for contact between different types of metals, which can lead to galvanic corrosion.
Inspect for Stress Points: Look for areas where the metal is under stress or subject to vibration, which can cause stress corrosion cracking.
Check for Microbial Growth: Inspect for the presence of microorganisms, especially in moist and nutrient-rich environments.
Early detection is key to preventing further damage and minimizing repair costs.
Repairing the Damage
Once rust and corrosion have been identified, it's time to take action. Here's the process I typically follow for repairing affected areas:
Step | Description |
---|---|
Remove Rust and Corrosion | Using mechanical methods like wire brushing, sanding, or grinding, I remove as much rust and corrosion as possible from the affected area. |
Clean the Surface | Thoroughly cleaning the area with a degreaser or solvent is crucial to remove any remaining contaminants that could interfere with the repair process. |
Apply Rust Converter or Primer | I then apply a rust converter or primer specifically designed for metal surfaces to prevent further corrosion and provide a solid base for subsequent coatings. |
Fill and Seal | For severe corrosion, I use a filler material like epoxy or body filler to rebuild the affected area, and then seal it with a protective coating. |
Paint or Coat | Finally, I apply a protective paint or coating suitable for the environment and intended use, ensuring a long-lasting repair. |
Throughout the repair process, I always work in a well-ventilated area and wear appropriate personal protective equipment (PPE) when handling chemicals or generating dust. Following the manufacturer's instructions for proper application and curing times of coatings and sealants is also essential for a successful repair.
In cases of severe corrosion, where repair is not feasible or cost-effective, I may recommend replacing the affected components entirely.
Preventing Future Rust and Corrosion
While repairing existing rust and corrosion is important, prevention is the key to avoiding costly and time-consuming repairs down the line. Here are some strategies I recommend for preventing rust and corrosion from recurring:
Regular Maintenance: Implementing a regular maintenance schedule for inspecting and cleaning metal surfaces, removing any accumulated dirt, moisture, or contaminants, is crucial.
Proper Storage: Storing metal components in a dry, well-ventilated area, and considering the use of desiccants or dehumidifiers to control moisture levels, can go a long way in preventing corrosion.
Protective Coatings: Applying protective coatings like paint, galvanizing, or plating to metal surfaces creates a barrier against corrosion and can significantly extend the lifespan of components.
Cathodic Protection: For buried or submerged metal structures, using cathodic protection systems can effectively prevent corrosion.
Avoid Dissimilar Metals: When possible, avoiding direct contact between dissimilar metals can prevent galvanic corrosion from occurring.
Proper Use and Operation: Following the manufacturer's guidelines for the intended use and operation of metal components or equipment can prevent excessive stress or exposure to corrosive environments.
By implementing these preventive measures, you can save yourself a lot of headaches and costly repairs down the road.
The Cost of Rust and Corrosion
The cost of repairing rust and corrosion can vary significantly depending on the extent of the damage and the method of repair. Some factors to consider include:
Cost Factor | Description |
---|---|
Labor Costs | Professional repair services can charge hourly rates ranging from $36 to $200 or more, depending on the complexity of the job. |
Materials | The cost of materials like rust converters, primers, fillers, coatings, and replacement parts can add up quickly. |
Equipment | If you choose to perform repairs yourself, you may need to invest in tools and equipment like angle grinders, wire brushes, and sandblasters. |
Preventive Maintenance | Implementing regular maintenance and protective measures can be more cost-effective in the long run by preventing extensive corrosion and extending the lifespan of metal components. |
It's essential to weigh the costs of repair against the value of the affected component or structure and consider the potential consequences of not addressing the issue, such as structural failure or safety hazards.
Conclusion
Rust and corrosion are silent but relentless enemies in the automotive world. As a mechanic, I've seen firsthand the devastating effects they can have on vehicles and the importance of taking proactive measures to prevent and address these issues. By understanding the causes, identifying the signs, and following proper repair and prevention techniques, you can protect your vehicle from the ravages of rust and corrosion, ensuring its longevity and safety on the road.
Remember, an ounce of prevention is worth a pound of cure. Regular maintenance, proper storage, and the application of protective coatings can save you from costly repairs and headaches down the line. Don't let rust and corrosion catch you off guard – stay vigilant, and your vehicle will thank you for it.
FAQs
What is the difference between rust and corrosion?
Rust is a type of corrosion that specifically affects iron and steel. Corrosion is a broader term that refers to the deterioration of any metal due to chemical reactions with its environment.
What causes galvanic corrosion?
Galvanic corrosion occurs when two different metals are in electrical contact in the presence of an electrolyte, causing one metal to corrode faster than the other.
How does salt accelerate corrosion?
Salt contains chloride ions that act as an electrolyte, facilitating the electrochemical reactions that lead to corrosion. This is why vehicles in coastal regions are more prone to corrosion.
What is stress corrosion cracking?
Stress corrosion cracking is a type of corrosion that affects metals under stress when exposed to corrosive environments, such as high temperatures or certain chemicals.
What is microbial corrosion?
Microbial corrosion is caused by microorganisms that produce acidic compounds, which corrode metal surfaces in the presence of moisture and nutrients.
What is fretting corrosion?
Fretting corrosion is a form of wear corrosion that occurs on surfaces in contact with each other during movement or vibration, creating small particles that can form an electrolyte and lead to further damage.
How can coatings prevent corrosion?
Coatings like paint, powder coatings, and plating create a barrier between the metal and the environment, preventing moisture and other corrosive substances from reaching the metal surface.
What is cathodic protection?
Cathodic protection is a technique used to control the corrosion of a metal surface by making it the cathode of an electrochemical cell.
How can corrosion inhibitors help?
Corrosion inhibitors are chemicals that interrupt the electrochemical processes that lead to corrosion, either by reacting with the metal surface or the surrounding environment.
Why is early detection of corrosion important?
Early detection of corrosion is crucial to prevent further damage and minimize repair costs, as corrosion can silently compromise the structural integrity of metal components over time.
Bình luận (0)
Bài viết đề xuất
The P001A diagnostic trouble code is a warning signal that indicates an issue with the camshaft profile actuator control circuit or an open circuit in Bank 1 of the engine. This code is specifically related to the variable valve timing system, which plays a crucial role in optimizing engine performance and efficiency.
Brake shoes are crescent-shaped metal components lined with friction material on one side. They are an integral part of the drum brake system, which is commonly used on the rear wheels of modern vehicles. The primary function of brake shoes is to create friction against the inside of the brake drum, slowing down or stopping the rotation of the wheels when the brakes are applied.
When all the warning lights on your car's dashboard illuminate simultaneously, it's a clear sign of an electrical problem, typically related to the charging system. This comprehensive guide will help you understand the causes, symptoms, and steps to address this issue effectively.